溶接には、外観の美しさだけでなく、接合の強度や耐食性、寸法精度などのさまざまな品質が求められます。品質が不十分だと、溶接した製品の使用中に破損や劣化を引き起こすリスクがあるため、慎重な品質管理が必要です。
とはいえ、接合部の内部が見えない溶接の品質は管理が難しく、「溶接品質を管理する方法がわからない」といった方も多いのではないでしょうか。
そこで本記事では、溶接品質の管理項目や検査方法について解説します。溶接品質の管理について学びたい方は、ぜひ参考にしてみてください。
溶接に求められる品質とは
溶接は、金属部材を接合する加工技術のひとつであり、自動車や建築、インフラ、プラント、造船など多くの産業において欠かせない工程です。そのため、溶接部の品質は製品全体の安全性・耐久性・信頼性を左右する重要な要素となります。
溶接における「品質」とは、単に見た目が美しいというだけではなく、接合部の強度や靱性、耐食性、欠陥の有無、寸法精度といった多岐にわたる性能のことです。溶接部が設計通りの性能を満たし、使用中に破損や劣化を引き起こさないことが求められます。
このため、溶接には事前の材料選定・適切な溶接条件の設定・作業者の技能・施工後の検査までを含めた厳格な品質保証体制が必要です。
溶接品質保証が難しい理由
溶接技術の品質確保は、機械加工などと比較して特に難しく、「特殊工程」として扱われることもあります。通常の検査・試験方法では、溶接部の健全性や品質を十分に検証することが出来ないためです。
溶接、表面処理、非破壊検査等、「特殊工程」とされる工程は、4M(Man, Machine, Material, Method) 、つまり、人、設備、材料、工程の管理が品質に大きくかかわります。
まず、溶接は「人の手」に大きく依存する工程であり、作業者の技量や姿勢、溶接条件のわずかな変化が品質に直結します。同じ手順で行っているつもりでも、環境の違いや体調によるブレが生じやすく、品質のばらつきを招くことがある点には注意が必要です。
次に、溶接による接合部は、金属を高温で溶かしながら固めるというプロセスを経るため、溶接中の熱の入り方や冷却速度により金属組織が変化しやすいという特性があります。この金属内部の変化は目に見えないため、外観だけで品質を判断することは困難です。
さらに、溶接は内部に気孔(ブローホール)やクラック(割れ)、スラグ巻き込みといった欠陥が生じやすく、それらが顕在化したときにはすでに製品として使われている場合もあります。こうした見えない欠陥の検出には専門的な非破壊検査技術が必要であり、検査や管理体制が複雑化する要因だといえるでしょう。
溶接品質の管理項目
溶接品質を安定させるためには、以下のような管理項目を的確にチェックすることが重要です。
<溶接品質の管理項目>
管理項目 | 説明 |
---|---|
外観品質 | ビードの幅、高さ、形状に異常がないか、スパッタやアンダーカットなどの外観不良がないか |
寸法精度 | 設計寸法と照らし合わせてズレがないか。熱による変形や歪みが生じていないか |
機械的特性 | 接合部が使用環境に応じた機械的性能(引張強度、疲労強度など)を有しているか |
溶接条件 | 電流・電圧・溶接速度・シールドガスの流量などが適正範囲にあるか。作業環境(湿度・風など)の管理も含む |
材料の適合性 | 母材や溶加材が規定の仕様に合致しているか。異種金属接合時の適合性も要チェック |
これらの項目は溶接前の工程設計・実際の施工中・施工後の検査工程でそれぞれ確認・管理されます。
外観品質
外観品質は、溶接品質の管理の初期段階で最も重視される項目です。ビード(溶接の盛り上がり)の形状や幅、高さに異常がないか、クラックやアンダーカット、スパッタの付着などの表面的な欠陥を目視で確認します。
見た目が整っていない場合は、内部にも問題がある可能性があるため、外観不良は重大な警告サインともいえます。また、仕上がりの美しさは製品の商業価値や顧客満足度にも関わるため、厳しい基準での確認が必要です。
寸法精度
溶接の過程では、熱の影響により部材が膨張・収縮するため、設計通りの寸法を保つのが難しい場合があります。そのため、溶接後に対象物が設計図と一致しているかの確認が必要です。
寸法誤差は組立工程の不具合や強度不足、最終製品の不良につながる可能性があります。とくに複数の部品を組み合わせる構造物や機械装置では、寸法管理が製品全体の精度や性能に大きく影響するため要注意です。
機械的性質(強度・靭性)
強度とは力を加えた際に破断しにくい性能であり、靭性は衝撃や急激な力にも壊れにくいしなやかさを指します。溶接部がこの2つの性能を備えていることは、安全性の確保において極めて重要です。
適切な溶接が行われていれば、母材と同等、またはそれ以上の強度を持つ接合部が形成されます。逆に、強度が不足していると、使用中に亀裂が入ったり破損したりして、重大事故を引き起こすリスクが高まるため、慎重な検査が必要です。
溶接条件
溶接に使用する電流・電圧・速度・シールドガスの種類と流量などは、品質に大きく影響する要因です。これらの条件が少しでもズレると、溶け込み不足・未溶着・割れ・ブローホールといった不具合が発生しやすくなります。
さらに、作業エリアの温度や湿度、風の有無などの作業環境も溶接品質に影響を与えるため、事前に条件を設定し、その通りに管理・記録することが欠かせません。
材料の適合性
使用する母材および溶加材が仕様に合致しているかも、品質保証上欠かせない項目です。材質が設計通りでない場合、溶接中に想定外の反応が起こり、ひび割れや欠陥の原因となります。
とくに異種金属の接合では、膨張係数や電位差などの考慮が必要です。
成分、強度、溶接性等を考慮して、使用する母材、溶接方法、溶加材を決定します。
特に、異種金属の溶接に当たっては、少しの成分で溶接性が大きく変わることもあります。実際に手配した材料が仕様に沿っているものなのか、材料証明書(ミルシート)等での確認、管理も必要となります。
溶接品質の検査方法
溶接品質を検証するための検査には、主に外観検査と各種非破壊検査(NDT:Non-Destructive Testing)があります。代表的な検査方法は以下のとおりです。
- 外観検査
- 磁粉探傷試験(MT)
- 浸透探傷試験(PT)
- 放射線透過試験(RT)
- 超音波探傷試験(UT)
外観検査
外観検査は、最も基本的かつ迅速に実施できる検査方法です。専用のルーペやゲージを使って、ビードの幅や高さ・焼けの程度・スパッタの付着・アンダーカット・クラックの有無などをチェックします。
外観上の異常は内部欠陥の兆候である場合もあり、最初のチェックポイントとして極めて重要です。とくに、高温で発生する変色(酸化)・ビードの均一性・過剰な盛り上がりや凹みなどは、品質のばらつきに直結するため、慎重に確認する必要があります。
外観検査は単体では限界があるため、他の検査と併用するのが基本です。
磁粉探傷試験(MT)
磁粉探傷試験(MT)は、鉄鋼などの磁性体に対して用いる表面欠陥の検査手法です。適用できる対象が磁性体のみ、という制約がありますが、部材を磁化した状態で磁粉(鉄粉)をまき、磁束の乱れによって磁粉が欠陥箇所に集まる現象を利用してきずを可視化します。
肉眼で見えにくい微細なクラックや表面割れも検出可能で、再現性や信頼性の高い検査法とされています。また、コストも比較的低く、作業性も良いため、多くの現場で活用されている検査手法です。
ただし、磁性体以外には使用できないため、材質による制限がある点には注意する必要があります。
浸透探傷試験(PT)
浸透探傷試験(PT)は製品表面の開口きずを確認する方法で、「染色探傷試験」と「蛍光探傷試験」の二種類の検査方法があります。
「染色探傷試験(カラーチェック)」は、赤色染料の浸透液を製品の表面に塗布した後、ふき取りを行い、白色現像液を吹きかけます。ピンホールやクラックなどのきずは毛管現象で浸透液が染み込んでいるため、白色バックグラウンドに赤い欠陥指示模様として浮かびあがります。特別な設備が不要なため、室内外、昼夜を問わずに試験を行うことが出来るという手軽さから、様々な材質、現場に広く適用されています。
「蛍光探傷試験」は、蛍光物質が添加されている探傷液を使用し、暗所で紫外線を照射して発光したきずを観察する方法です。染色探傷試験よりも検査精度が高いとされますが、紫外線照射装置や暗室等、専用設備が必要となります。主に航空機部品等に適用されている技術です。
一方で、両方の技術の欠点として、欠陥の深さまでは判断できない点が挙げられます。
放射線透過試験(RT)
放射線透過試験(RT)は、X線やガンマ線といった放射線を対象物に照射し、その透過画像を用いて内部欠陥を検出する検査方法です。ブローホール・スラグ巻き込み・未溶着などの内部欠陥を非破壊で検出できます。
フィルムを使うアナログ方式のほか、近年ではデジタルRTも普及しており、即時に画像解析が可能です。一方、専門設備と放射線管理の知識が必要で、安全面やコスト面でのハードルがあります。
超音波探傷試験(UT)
超音波探傷試験(UT)は、溶接部に超音波を送信し、反射波を受信して内部の欠陥を検出する非破壊検査方法です。厚みのある部材や複雑な形状にも対応でき、深部の欠陥まで検出できる点が特徴だといえます。
欠陥の大きさ・位置・深さを三次元的に把握できることから、高度な検査として位置づけられています。機器が小型で携帯性にも優れ、屋外や高所での検査も可能です。
ただし、反射波の解釈には熟練した技術者の判断が必要で、材質や形状により検出精度が変動するため、訓練が不可欠である点には注意しましょう。
まとめ
本記事では、溶接における品質とは何か、品質管理が難しい理由などとあわせて解説しました。溶接品質は製品の強度などを担保するうえで重要でありながら、溶接の品質はほかの工法と比べると管理が難しいのが特徴です。
溶接品質の管理項目としては、外観品質・寸法精度・強度・靭性・溶接条件・材料の適合性などが挙げられます。これらを検査する方法には、外観検査・磁粉探傷試験(MT)・浸透深傷試験(PT)などの方法があり、適切な検査方法の採用が必要です。
金属技研では、約20種類以上の充実した検査項目と、最新鋭検査装置を導入した非破壊検査を提供しています。溶接品質の管理・検査でお困りの方は、ぜひ当社にご相談ください。
セミナー紹介
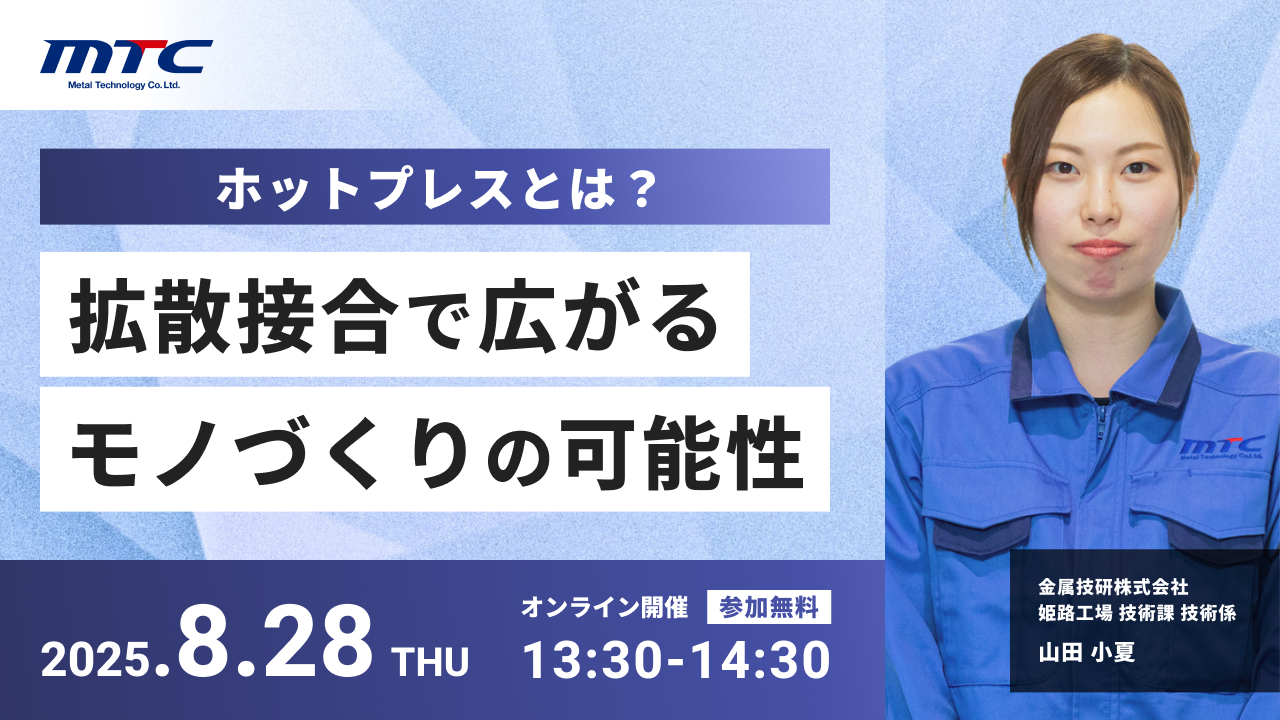