圧接は、金属等の母材に圧力をかけて接合する固相接合方法です。母材を溶融させて接合する「融接」(アーク溶接、レーザー溶接、電子ビーム溶接等)と比べると、熱による影響が少なく、母材の特性を維持しやすい点等が利点として上げられます。
ただし、圧接にはいくつか種類があり、それぞれ異なる原理を持つため、「圧接とは何なのか、より詳しく知りたい」といった方も多いのではないでしょうか。
そこで本記事では、圧接とは何か、代表的な施工法やそのメリット・デメリットなどについて解説します。溶接との違いにも触れるので、ぜひ参考にしてみてください。
なお、圧接の種類や工法、メカニズムは多岐に渡ります。本記事では、技術や業界に関する一般的な傾向や考え方をご紹介しています。特定の学術的理論や個別の生産現場に基づいた内容ではなく、あくまで参考情報としてご覧いただければ幸いです。
圧接とは
圧接とは、金属などの母材を加圧することで接合面を原子レベルで密着させ、接合する固相接合法の一種です。溶接のように母材を完全に溶融させることなく、加熱と圧力、あるいは摩擦や爆発などのエネルギーによって、材料の境界面を接合します。
圧接においては、母材の接合面に酸化被膜などの不純物があると接合強度に悪影響を及ぼすため、接合面を十分に清浄化する工程が必要です。接合は、材料の塑性変形を活用して接触部に十分な接合圧をかけ、表面の酸化物や異物を排除しつつ、接合を促進します。
このような圧接技術は、鉄筋・パイプ・導線・クラッド鋼などの接合に広く使用されています。
圧接と融接の違いは?
圧接と融接は、いずれも金属を接合する方法ですが、プロセスにおける大きな違いがあります。最大の違いは「母材を溶かすかどうか」です。
融接では、母材そのもの、あるいは接合補助材(溶加材/棒)を高温で溶かして、接合部を一体化させます。アーク溶接やガス溶接、レーザー溶接などがその代表例です。一方、圧接では、材料を溶かすことなく、加圧や熱処理、あるいは摩擦や爆発などのエネルギーを用いて金属を密着させて接合します。
もう一つの違いは、熱による影響の大きさです。溶接では高温で母材の一部を溶かすため、熱による変形や局所的な強度低下のリスクがあります。一方、圧接ではそれが比較的少なく、接合部の物性を維持しやすいのが利点です。
圧接の種類
ここでは代表的な圧接の方法として、以下の5種類の方法について解説します。
ガス圧接
ガス圧接は、酸素とアセチレンなどの可燃性ガスを用いて接合部を赤熱状態に加熱し、その後すばやく圧力をかけて接合する方法です。鉄筋やパイプの接合で広く用いられています。
ガス圧接は、数ある圧接のなかでも比較的単純な装置で行えるため、工事現場や土木建築分野で多用されている方法の1つです。加熱後すぐに圧力をかけることで、材料同士の表面が塑性変形し、酸化被膜などが押し出され、金属の結晶構造が連続して接合されます。
ガス圧接は、鉄筋を接合する場面でも使われており「ガス圧接継手」と呼ばれています。強度的にも溶接に引けを取らない接合が可能ですが、作業者の技量で品質が大きく左右されるため、JIS Z 3881に基づく技量資格認定を受けた技量者のみが施工できます。
摩擦圧接
摩擦圧接は、片方または両方の母材を高速回転させ、その回転運動による摩擦熱と圧力で接合面を軟化させたうえで加圧し、接合する方法です。接合中は溶融を伴わず、金属が塑性状態で接合されます。
摩擦圧接では回転による熱の発生が主なエネルギー源となるため、電力のみで加熱が可能です。
施工時間が短く作業能率が高いこと、圧接機や圧接条件、材料等の管理を十分に行えば再現性が良好であることに加え、摩擦圧接は異種金属同士の接合にも比較的適しています。
自動車や航空機、建機部品などの量産分野や、異材間の機械的な接続が求められる分野でも重宝されている方法の1つです。
一方、摩擦圧接の制約として、接合する材料(少なくとも片側)は、丸棒、パイプなどの円形断面とする必要があること、薄肉のパイプは接合困難であることなどが挙げられます。
抵抗圧接
抵抗圧接は、母材に電流を流すことで発生する電気抵抗熱を利用して接合面を加熱し、その後加圧して接合する方法です。スポット溶接やシーム溶接などがこの方式に含まれます。自動車ボディの製造や家電製品の筐体など、板金部品の接合に広く使用されている方法です。
抵抗圧接は、金属の接触部分に局所的な熱が集中するため、熱の影響を最小限に抑えることができます。また、装置の自動化がしやすく、高速で連続的な溶接が可能なため、量産に向いた工法です。
拡散接合
拡散接合は、高温かつ真空環境下で母材を接触させ、原子の拡散を利用して接合する高度な圧接技術です。高精度かつ高強度な接合が可能で、半導体部品・センサー・医療機器などの精密分野で利用されています。
拡散接合は、異種金属や複雑形状の接合も可能な接合技術ですが、接合面の状態や接合温度、圧力などが接合強度に大きく影響します。
そのため、専用の設備(HIP・ホットプレス等)と専門知識が必要となる接合技術です。
HIP(熱間等方圧加圧)装置による拡散接合は、高圧ガスを用いる手法で、曲面や配管等との三次元的な接合が可能です。
爆発圧接
爆発圧接(爆着)は、火薬の爆発エネルギーを利用して、2つの金属を一瞬で高速かつ高圧で衝突させ接合する工法です。通常では接合が難しい異種金属の接合に効果を発揮し、とくに金属クラッド材(異なる金属の積層材)などの製造に使われます。
この方法は瞬間的な接合で熱影響が少なく、母材の物性が損なわれにくいのが利点です。ただし、安全管理や取り扱いに高度な専門性が求められ、一般的な工場での常用には不向きとされます。
圧接のメリット
圧接の主なメリットとして、以下の5点を解説します。
- 母材の特性を維持できる
- 異種金属の接合に対応できる
- 作業環境がクリーン
- 高強度な接合が可能
- 自動化・省人化がしやすい
母材の特性を維持できる
圧接は、母材を溶かすことなく圧力や熱で接合する方法です。アーク溶接のような融接と比較して、金属組織の局所的な劣化が少ないため、母材の強度や靭性を大きく損なうことなく接合することが可能です。
ただし、拡散接合のような材料全体を加熱する処理方法では、母材全体が焼き鈍し状態となり、強度が下がります。そのため、焼鈍状態の母材および接合部が要求される強度を満足するか、事前の検証が必要です。
異種金属の接合に対応できる
圧接は、溶接では困難とされる異なる金属材料同士の接合にも対応できます。とくに摩擦圧接・爆発圧接・拡散接合などは、鉄とアルミ、チタンとステンレスなど、性質が異なる金属を強固に接合することが可能です。異種金属の組み合わせを活用することで、軽量化や耐食性の向上など、製品設計の自由度が大きく広がります。
作業環境がクリーン
圧接は火花やスパッタが発生しない、あるいは少ないため、作業中の安全性が高く、作業環境もクリーンに保ちやすいのが特徴です。また、煙や有害ガスの発生がほとんどないため、溶接と比較して安全性の高い作業環境を実現できます。
高強度な接合が可能
圧接では、接合部が材料同士の原子レベルで密着するため、接合後の引張強度やせん断強度が高くなります。とくに摩擦圧接や拡散接合では、高強度に接合できるため、信頼性が重要視される構造部品や重要な機械部品などにも採用可能です。
自動化・省人化がしやすい
摩擦圧接や抵抗圧接などの圧接方法は、ロボットや自動装置による自動化がしやすい点が大きなメリットです。作業の熟練度に依存しにくく品質を一定に保てるため、量産品や連続生産ラインにも適しており、省人化・効率化に貢献します。
圧接のデメリット
圧接の主なデメリットとして、以下の5点を解説します。
- 専用設備が必要でコストが高い
- 求める形状に適した接合方法の選択を
- 接合条件の管理がシビア
- 接合部の健全性確認が困難
- 設備や作業に高度な安全対策が必要
専用設備が必要でコストが高い
圧接には、加圧装置や制御機器、高温を発生させる加熱機構など、用途に応じた専用設備が必要です。とくに摩擦圧接や拡散接合、爆発圧接などは初期導入コストが高く、維持管理にも専門的な知識が求められます。中小規模の製造現場では導入のハードルとなることも多いでしょう。
求める形状に適した接合方法の選択を
圧接は様々な方法で加圧を行うため、製品の形状や求められる仕様によって適用可能な工法が異なります。
例えば、摩擦圧接は基本的に円形形状であること、爆発圧接は平面またはパイプ状であること等、形状の制約があります。曲面や入り組んだ接合形状であればHIP拡散接合、微細な水路構造を求める場合はホットプレス拡散接合が適しています。
また、接合(接触)面積が小さい場合や、硬さや熱膨張率が大きく異なる材料の接合では、強度のばらつきや著しい変形が生じるリスクがあります。
接合条件の管理がシビア
圧接はいわゆる特殊工程と呼ばれる手法であり、徹底した4M管理(Man、Machine、Method、 Material)が求められます。
Man:ガス圧接のような手動による接合手法では、施工者が有資格者に限られています。
Machine、Method:温度・加圧時間・接触圧力の過不足は接合不良や強度不足に繋がります。事前試験により決定した施工(接合)方法を遵守するため、設備および工程の管理が求められます。
Material:同じ材種の金属でも、添加元素や製造方法の違いが接合可否や強度に大きく影響する場合があります。そのため、この製品にはこのメーカーの材料のみを使用する、と限定しているケースも。これは特殊な例ですが、一般的な製品においても、材料証明書(ミルシート)の確認、管理を確実に行う必要があります。
接合部の健全性確認が困難
接合部の内部にある空隙や未接合部は、接合強度や品質に重大な影響を与えます。接合部の健全性を確認する代表的な手法として、①リーク検査(漏れ試験)②RT、UTなどの非破壊検査の二つが挙げられます。
①リーク検査
接合部にガスを流し込み、漏洩の有無を検出する漏れ検査です。接合部に石鹸水を塗布してリーク部分に発生する泡を確認する簡易的な方法や、Heガス検出器を用いる方法等があります。
重要な点は、この検査で確認できるのは「密封出来ているか」であり、接合強度の保証にはならないこと、そして、封止できる構造にしか適用できないことです。
例えば、クラッド材のような板形状にはリーク検査は適用出来ません。また、リーク検査用に専用の治具が必要となることがあります。
②RT,UT等の非破壊検査
接合部の内部に空隙や未接合部が存在するかを、放射線や超音波を使って確認します。
想定されるきずの形状や、検査対象物の材質や形状によって適切な検査方法が異なること、厚さや材質によっては検出が困難であることなどから、適用にあたっては検査担当者との事前調整が必要です。
上記以外の確認方法として、接合部の一部を切り出したり、同一ロットからサンプルピックアップを用いて破壊試験を行う等の方法があります。
これらの手法を複数組み合わせる場合もあるため、検査工程の負担やコストが増大する可能性があります。
設備や作業に高度な安全対策が必要
爆発圧接や高電流を扱う抵抗圧接など、一部の圧接法では大きなエネルギーを短時間に加えるため、操作ミスや設備故障が事故につながるリスクがあります。そのため、作業者の教育や適切な安全管理体制が不可欠です。
まとめ
本記事では、圧接とは何か、溶接との違いや種類について解説しました。圧接は、金属などの母材を加圧することによって、接合面を密着させる固相接合法です。ガス圧接・摩擦圧接・爆発圧接(爆着)・拡散接合などが該当します。
圧接は溶接とは違い、材料への熱による影響が少ない点などが特徴です。高強度な接合ができ、自動化しやすい点もメリットだといえます。一方、専門的な設備が必要となるため、導入コストが高い点には注意が必要です。
金属技研では、幅広い材料・形状の材料を高強度に接合できるHIPおよびホットプレス装置を用いた拡散接合を提供しています。圧接や拡散接合に関してお困りの方は、ぜひ当社にご相談ください。
セミナー紹介
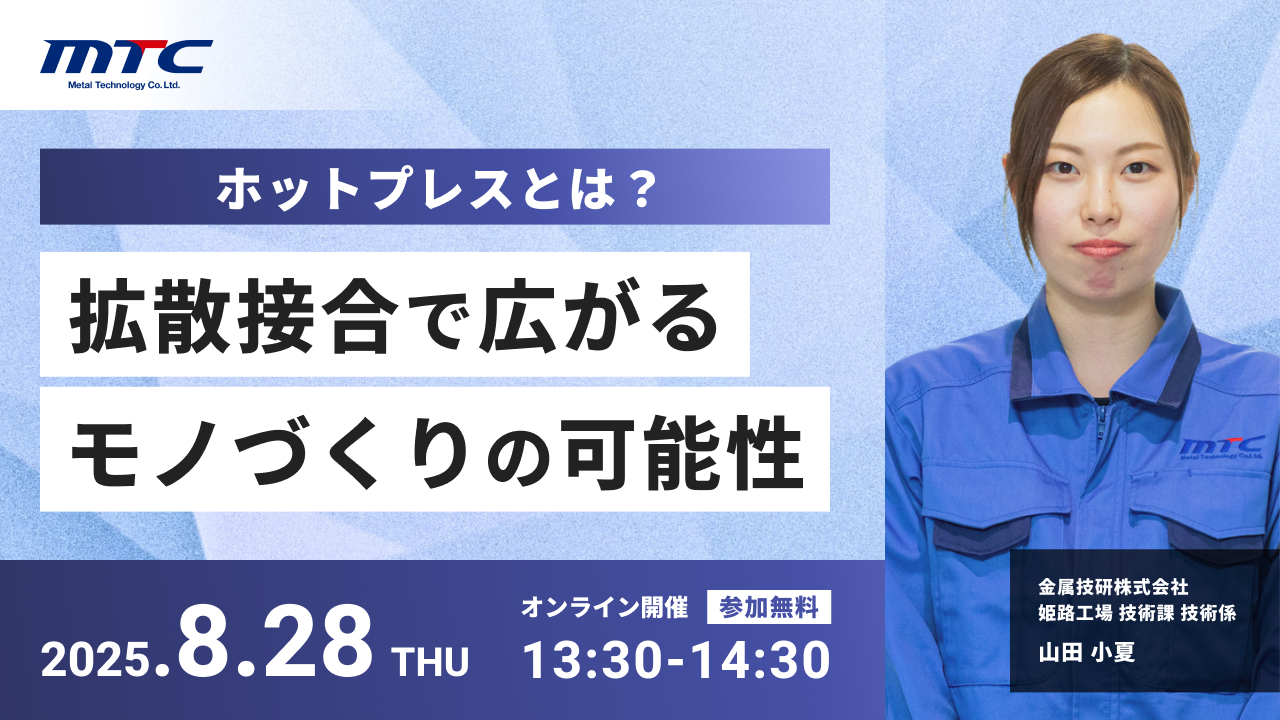