レーザー溶接はレーザー光を接合部に集中させて局所的に加熱し、材料同士を接合する溶接方式です。精度の高い溶接が可能で、溶接部分もきれいに仕上がることから、精密機器部品の接合などにも使われます。
この記事では、レーザー溶接とはどんな技術なのか、特徴や使用例、メリット・デメリットなどを解説します。レーザー溶接技術について理解を深めたい方は、ぜひ参考にしてください。
レーザー溶接とは
レーザー溶接とは、高出力のレーザー光を金属などの接合部に集中的に照射し、局所的に加熱・溶融して接合する溶接方法です。レーザー(Light Amplification by Stimulated Emission of Radiation)は、波長のそろった光を一点に集光でき、高いエネルギー密度を持ちます。
レーザー溶接では、母材表面に集光されたレーザー光が金属に吸収され、瞬時に高温となることで溶融池が形成されます。これが冷却・凝固すると、部材同士が接合されます。溶融させる深さや範囲は、レーザーの出力・照射時間・集光条件によって精密に制御可能です。
使用されるレーザーには、CO2レーザー・YAGレーザー・ファイバーレーザーなどがあり、接合対象の材質や精度要件に応じて選定されます。また、レーザー照射は非接触で行われるため、工具摩耗がなく、微細部位にも適用可能です。
レーザー溶接の特徴
レーザー溶接の主な特徴としては、以下の4点が挙げられます。
局所加熱により精密で歪みの少ない溶接が可能
レーザーは狭い範囲にエネルギーを集中できるため、局所加熱によりほかの領域への熱影響を最小限に抑えられます。周囲に歪みや変形を与えにくく、熱による素材特性の劣化も抑制可能です。
また、ビーム径や出力は精密に制御可能で、数ミクロン単位の微細溶接にも対応できます。そのため、薄板部品や精密機器の接合でも安定して溶接できるのが特徴です。
異種金属の接合にも対応しやすい
レーザー溶接は、溶接対象の金属表面のみを短時間で溶融させます。そのため、熱膨張率の異なる材料同士でも割れが生じにくいのが特徴です。たとえば、銅とアルミニウム、鉄とニッケルなど、通常の溶接では難しい異種金属の接合にも適用できます。
目的に応じた溶接方式を選べる
レーザー溶接には、目的や部品形状に応じて複数の溶接方式があります。
ごく短時間で一点を接合する「スポット溶接」は、電子部品やバッテリー端子など微細部品の接合に最適です。一方、トーチを連続的に動かしながら溶接する「シーム溶接」は、密閉性や外観の美しさが求められるケースに適しています。
また、高出力レーザーによって深く溶け込ませる「キーホール型溶接」は厚板や高強度部材の接合に用いられ、熱伝導によって表層だけを溶かす「熱伝導型溶接」は、薄板や熱に弱い部材に適しています。こうした方式を柔軟に使い分けられる点も、レーザー溶接の特徴です。
装置の小型化・自動化が容易
レーザー溶接は、装置の構造がシンプルで、電子ビーム溶接のような真空チャンバーを必要としません。そのため、レーザー溶接機は設置スペースが小さく、省スペース化が求められる製造現場でも導入しやすいといえるでしょう。
さらに、レーザーは光学ファイバーで伝送できるため、ロボットなどとも比較的容易に連携できます。溶接位置やパラメータはコンピュータ制御で細かく調整可能であり、複雑な工程でも完全自動化による連続運転が可能です。
レーザー溶接の使用例
レーザー溶接の使用例を3つ紹介します。
電気自動車(EV)バッテリーの製造
レーザー溶接は、EVバッテリーの製造において不可欠な技術です。とくにバッテリーセルとバスバーの接合では、異なる金属材料の高精度かつ高速な溶接が求められます。
レーザー溶接は、非接触でエネルギーを集中させられるため、熱影響を最小限に抑えつつ、強固な接合が可能です。これにより、電気自動車用バッテリーの生産効率も高まります。さらに、レーザー溶接は自動化が容易であり、大量生産にも対応可能です。
電子部品の微細溶接
スマートフォンやタブレットなどの電子機器では、微細な部品の高精度な接合が求められます。レーザー溶接は、極小のスポットサイズでエネルギーを集中させられるため、微細な部品の溶接に適しています。
たとえば、コネクタやカメラモジュール、振動モーターなどの部品の接合には、レーザー溶接が利用されています。また、非接触での溶接が可能なため、部品への物理的なストレスを抑えることが可能です。これにより、製品の品質と耐久性の向上が期待できます。
自動車ボディの溶接
自動車の車体製造においても、レーザー溶接は重要な役割を果たしています。とくに、異なる厚さや材質の鋼板を接合する際に、レーザー溶接による高い接合強度ときれいな仕上がりが役立ちます。
また、レーザー溶接は高速での加工が可能であり、生産ラインの効率化が可能です。さらに、ロボットアームとの組み合わせにより、複雑な形状や狭いスペースでの溶接も容易に行えます。
レーザー溶接のメリット・デメリット
レーザー溶接のメリットとデメリットを紹介します。
レーザー溶接のメリット
レーザー溶接の主なメリットは、以下の3つです。
変形を抑えつつ十分な強度の接合ができる
レーザー溶接は、狭い範囲に高エネルギーを集中できるため、母材全体への熱の影響を最小限に抑えられます。これにより、溶接による熱変形や歪みが起こりにくく、精密な製品にも対応可能です。
キーホール型などを用いれば十分な溶け込みと接合強度も確保できるため、軽量化や高剛性が求められる製品にも活用しやすいでしょう。
工数が削減でき生産性の向上が期待できる
レーザー溶接は熱歪みが小さいため、アーク溶接で必要となる歪み取り作業を省略できます。また、基本的に母材同士を直接接合するため、肉盛りが不要で、研磨工程も省略可能です。
さらに、加工条件を最適化することで溶接焼けも抑えられれば、電解研磨の工程を削減できます。こうした後処理工程の省略は、生産性向上だけでなく、製造コストの低減にも大きく貢献するでしょう。
条件管理がしやすく自動化に適している
レーザー溶接は出力・波形・照射時間などをデジタル制御できるため、加工条件の数値管理とトレーサビリティの確保が容易です。同じ条件で何度でも再現できるため、品質のばらつきが少なく、品質保証もしやすくなります。
また、光ファイバー伝送によりロボットとの相性もよく、フルオートメーション化にも対応できる点が大きな利点です。
レーザー溶接のデメリット
レーザー溶接のデメリットとしては、主に以下の4点が挙げられます。
安全対策が必須
レーザー溶接では、高出力のレーザー光を扱うため、目や皮膚への影響を防ぐ安全対策が欠かせません。レーザー遮蔽カバーの設置・ゴーグルの着用・インターロック装置の導入などが必要となり、作業者や設備周辺の安全管理コストがかかります。また、取扱者にはある程度の専門知識も必要です。
接合面に隙間があると溶接不良が起きやすい
レーザー溶接は精密なビームを使うため、接合面に隙間や不均一があると光が反射・逸脱し、十分に熱が伝わらず、溶接不良を引き起こす可能性があります。
とくに薄板や異種材の接合では、事前に正確な位置合わせやギャップ管理が重要となります。溶接前の加工精度が品質に大きく影響する点には注意しましょう。
表面状態に影響を受けやすい
レーザー溶接では、金属表面でのレーザー光の反射や吸収特性が加工精度に大きく影響します。汚れ・油分・酸化皮膜などが付着していると、レーザーが十分に吸収されず、溶け込み不足や欠陥の原因となります。
とくに高反射材(アルミや銅)では反射率が高く、表面処理が不十分だと照射エネルギーの多くが反射され、溶接が安定的に行えません。そのため、表面の前処理の徹底が重要な工程となります。
導入コストが高い
レーザー溶接を導入するには、高出力レーザー発振器・光学系・制御装置・冷却設備など、多くの高性能機器が必要です。そのため、初期導入コストはアーク溶接などと比べて高額になる傾向があります。
まとめ
本記事では、レーザー溶接について解説しました。レーザー溶接は、局所加熱が可能な点や出力を制御しやすい点などから、電気自動車のバッテリー・電子部品などさまざまな用途に活用されています。設備コストや安全対策が必要にはなるものの、精度が必要な溶接シーンではとくに効果を発揮するでしょう。
金属技研は、さまざまな溶接方式に対応しており、レーザー溶接機も所有しております。レーザー溶接に関するお困りごとがあれば、ぜひ当社にお問い合わせください。
金属技研の溶接技術についてはこちら
セミナー紹介
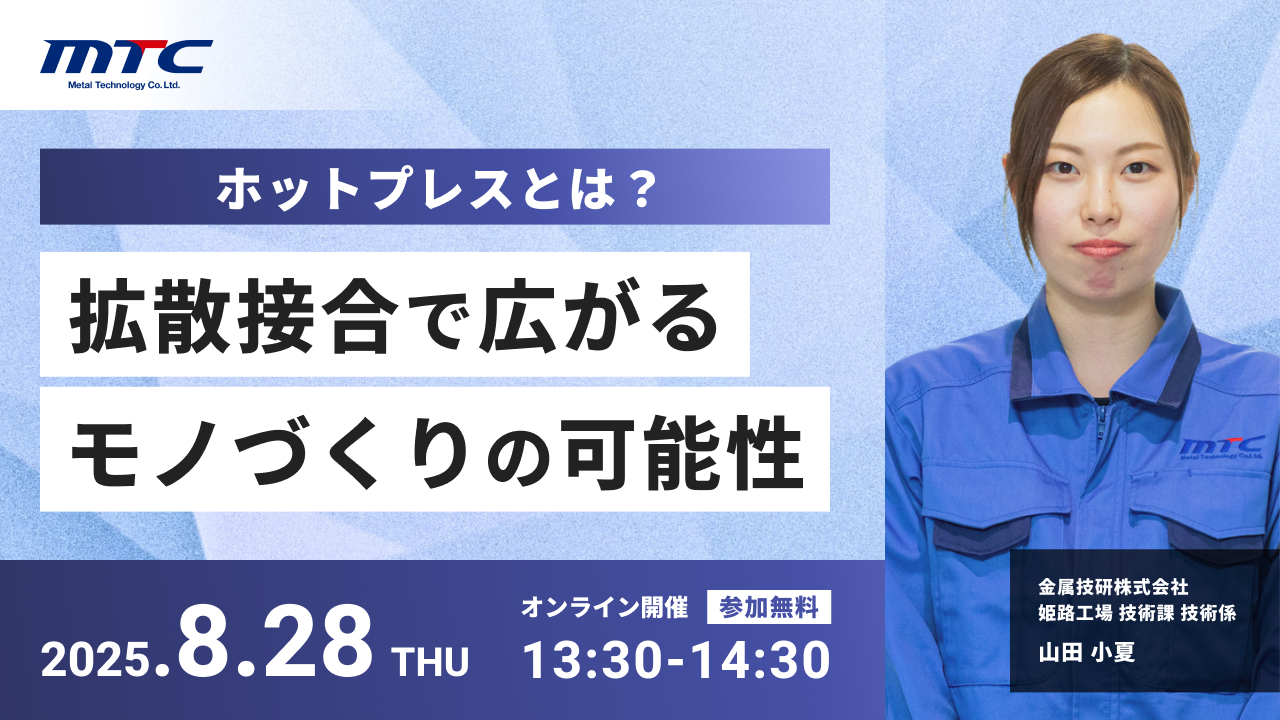