アルミニウムは、軽量で腐食しにくく加工しやすいことなどから、さまざまな用途に使用される金属です。ただ、溶接が難しい金属としても知られており、アルミ溶接をする際には適切な方法を選定する必要があります。
本記事では、アルミの基礎的な知識やアルミ溶接の方法について解説します。一般的に用いられるアルミ溶接の方法についてメリットやデメリット、主な用途なども紹介するので、ぜひ参考にしてください。
アルミの基礎知識
アルミニウムは、酸化アルミニウムを主成分とするボーキサイトという鉱石から生成される金属です。軽さや高い耐食性といった特徴を持つことから、さまざまな用途に活用されています。
特徴 | 説明 |
---|---|
軽量 | 鉄の約3分の1の比重で軽い |
耐食性が高い | 表面に形成される酸化皮膜により腐食しにくい |
加工が容易 | 展延性が高く、押出成形やプレス加工がしやすい |
熱伝導性・電気伝導性が高い | 銅には劣るものの、熱や電気を伝えやすい |
アルミの用途例としては、飲料の缶や車・飛行機といった輸送機器、電子機器部品まで幅広いものが挙げられます。リサイクル性の高さも魅力で、アルミ缶リサイクル協会によると、2023年のアルミ缶のリサイクル率は97.5%です。
アルミの種類
アルミにはいくつかの種類があり、それぞれ特徴や用途が異なります。アルミの主な種類と特徴、用途例は以下の表のとおりです。
種類 | 特徴 | 用途例 |
---|---|---|
純アルミニウム(1000系) | 軽量・高耐食性・加工が容易 | 熱交換器・電子機器 |
Al-Cu合金(2000系) | 高強度・低耐食性 | 航空機・自動車 |
Al-Mn合金(3000系) | 高耐食性・成形が容易 | 外装材・調理器具 |
Al-Si合金(4000系) | 高耐熱性・低膨張 | 自動車 |
Al-Mg合金(5000系) | 高耐食性・高溶接性 | 船舶・建材 |
Al-Mg-Si合金(6000系) | 高強度・高耐食性・加工が容易 | 建材・車両 |
Al-Zn合金(7000系) | 高強度 | 航空機・自動車 |
その他合金(8000系) | 高剛性・圧延加工性など種類による | 特殊用途 |
溶接しやすい材料としては、5000系が代表的です。たとえばA5052のアルミ合金は切削性と強度のバランスがよく、市場に多く流通しているアルミ合金のひとつです。純アルミに近いA1050も溶接に適しています。
一方、7000系は高強度が魅力ではあるものの、クラックがおきやすいため溶接には向きません。このように、アルミの種類によって溶接をするか別の方法を採用するかを判断する必要があります。
アルミの溶接が難しい理由
一般的にアルミは溶接が難しい素材だといわれています。アルミの溶接が難しい理由は以下のとおりです。
融点が高い酸化皮膜が生成されやすい
アルミは、空気中に放置しておくだけでも表面に酸化皮膜を生成するのが特徴です。アルミの酸化皮膜の融点は約2,000℃と非常に高く、アルミの融点の約660℃と大きな差があります。
そのため、溶接時にこの酸化皮膜が邪魔をして、うまく接合しない可能性があります。
アルミ溶接では、事前に酸化皮膜を除去するなどの対策が必要です。
融点が低いため溶けてしまいやすい
前述のとおりアルミの融点は約660℃で、融点が1,400〜1,450℃ほどのステンレスなどと比べると低いのが特徴です。溶接で熱をかけるとすぐに溶けてしまい、材料に意図しない穴が空いてしまうなどのリスクがあります。
そのため、アルミ溶接ではシビアな温度管理が必要です。適切な電流調整や予熱などの対策が求められます。
熱伝導性の高さにより歪みやすい
アルミは熱伝導性が高いため、溶接時の熱が周辺に一気に広がります。これによって、溶接部周辺まで加熱による変形・歪みが起きやすい点には注意が必要です。また、冷却時に収縮が大きく、残留応力や寸法誤差の原因になります。
そのため、溶接順序の工夫や治具による固定などの対策が必要です。予熱を適切に行ったり、均一に冷却したりするといった対策も挙げられます。
溶接割れが起こりやすい
アルミは熱膨張性が高く、脆くなる温度帯では亀裂が入りやすくなる点が特徴です。また、急激に冷却されたり、内部応力が集中したりすると割れ(クラック)が入りやすくなります。とくに厚板や複雑な形状の部材は、こうした溶接割れの発生リスクが高いといえるでしょう。
そのためアルミ溶接では、温度をはじめとした適切な接合条件の設定はもちろん、ひずみを逃がす構造設計が求められます。
アルミ溶接の方法
アルミ溶接にはさまざまな方法があります。ここでは、代表的なアルミ溶接の方法として、TIG溶接・半自動溶接・レーザー溶接について解説します。
方法 | 特徴 | 向いている用途の例 |
---|---|---|
TIG溶接 | 高品質で接合部の見た目がきれいに仕上がる | 精密機器や装飾部品など |
半自動溶接 | 作業性がよくスピーディに接合できる | 車両や構造物など |
レーザー溶接 | 高精度で熱影響が少ない | 精密部品やバッテリーケースなど |
TIG溶接
TIG(Tungsten Inert Gas)溶接とは、不活性ガスであるアルゴンとタングステン電極を用いる溶接方法です。アーク溶接に分類され、溶接棒を供給しながらアーク熱で母材と棒を同時に溶かして接合します。
アルミ溶接にTIG溶接を採用するメリット・デメリットは以下のとおりです。
<アルミ溶接にTIG溶接を採用するメリット>
- 溶接線がきれいで見た目の仕上がりがよい
- 熱入力を細かく調整できるため薄板にも対応できる
- 皮膜を剥がしながら溶接できるため酸化皮膜に強い
<アルミ溶接にTIG溶接を採用するデメリット>
- 時間がかかるため量産には向かない
- 手動の部分が多く熟練した技術が求められる
- 機械化が難しく自動化しづらい
TIG溶接で使うタングステン電極は溶けないため、アークが一点に集中し熱の入れ方をコントロールしやすいのが特徴です。そのため厚板だけでなく薄板にも対応でき、接合部がきれいに仕上がります。アークで皮膜を剥がしながら溶接できるのもポイントです。
一方、作業の大部分を手作業で行うため、量産や機械化・自動化には不向きです。また、高品質に仕上げるためには熟練した高い技術力が求められます。
半自動溶接
半自動溶接とは、溶接ワイヤー(アルミ合金)を自動で送り出し、アーク熱で母体とワイヤーを同時に溶かしながら溶接する方法です。半自動溶接にはいくつか方法がありますが、アルミ溶接においてはMIG(Metal Inert Gas)が使われます。
アルミ溶接に半自動溶接(MIG溶接)を採用するメリット・デメリットは以下のとおりです。
<アルミ溶接に半自動溶接(MIG溶接)を採用するメリット>
- 自動でワイヤーが送り込まれるため効率的に溶接できる
- 溶融量が多く厚板にも対応しやすい
- ロボット溶接に適用しやすく自動化しやすい
<アルミ溶接に半自動溶接(MIG溶接)を採用するデメリット>
- TIG溶接と比べると金属の飛び散り(スパッタ)が発生しやすい
- 熱入力が大きいため薄板の接合が難しい
- 酸化皮膜による接合不良が起きやすい
半自動溶接は、TIG溶接よりもスピーディに作業が進められるため量産にも向いています。ロボット溶接などと組み合わせれば、作業の自動化を図ることも可能です。溶融量が多いため、厚板もしっかり溶接できる点もメリットだといえます。
一方、TIG溶接と比べるとスパッタが発生しやすい点には注意が必要です。また、熱入力が大きいため、薄板に使うと溶け落ちてしまうリスクがあります。酸化皮膜による悪影響を受けやすいため、前処理が必要になる点にも要注意です。
レーザー溶接
レーザー溶接は、高出力レーザーによって金属表面を局所的に加熱・溶融して接合する方法です。CO2レーザーやファイバーレーザーが使用され、出力などは自動制御されます。
アルミ溶接にレーザー溶接を採用するメリット・デメリットは以下のとおりです。
<アルミ溶接にレーザー溶接を採用するメリット>
- 精密かつ高速で接合できる
- 局所的に加熱するため歪みや変形が生じにくい
- バリやスパッタが出にくくきれいに仕上げやすい
<アルミ溶接にレーザー溶接を採用するデメリット>
- 高価なレーザー装置が必要になり設備コストが高い
- 反射率が高いアルミでは表面処理の影響を受けやすい
- 厚板の処理には不向き
レーザー溶接のメリットは、精密かつ高速できれいな接合ができる点です。ミクロン単位の狭い接合部にも対応できるため、精密機器などに適しています。熱伝導性が高いアルミでは注意が必要ではあるものの、局所加熱するため歪みや変形が生じにくいのもメリットです。
ただし、レーザー溶接に使う設備は高価なのでコストがかかります。また、反射率の高いアルミに使う場合、表面処理の影響を受けやすいのも注意点です。半自動溶接やTIG溶接と比べると、厚板には対応しにくい点も理解しておきましょう。
まとめ
本記事では、アルミの基礎知識やアルミ接合の方法について解説しました。アルミ接合にはTIG溶接や半自動溶接、場合によってはレーザー溶接などの方法が採用されます。それぞれのメリット・デメリットを理解したうえで、用途に適した方法を用いることが重要です。
金属技研は、TIG溶接や半自動溶接(MIG溶接)、レーザー溶接の設備を保有しております。アルミ溶接でお困りの際は、ぜひお気軽にご相談ください。
金属技研の溶接技術についてはこちら
セミナー紹介
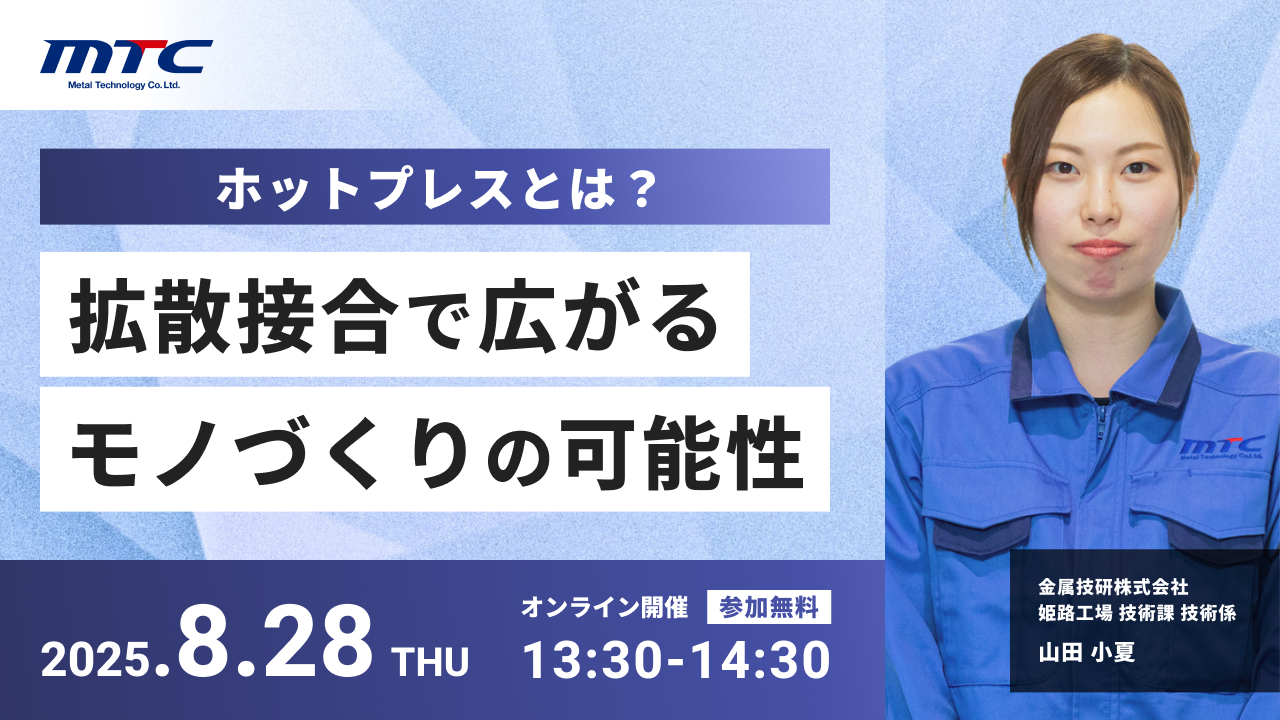