金属技研の歩み
History of MTC
History
歩み
1960年の設立以来、金属加工業界のリーディングカンパニーとして成長を続けてきた金属技研。
半世紀以上にわたる歴史を、ここで紹介します。
1960-70年代
創生期
熱処理事業の立ち上げと拡大
1960年、金属技研は、理化学研究所の(旧)金属工学研究グループが東京都板橋区に炉壁耐火煉瓦や配管工事など自前でこしらえた「ピット炉」を設置し、スタートしました。
『和を貴び、和を守る』という理念のもと、創業当時はフェライトの磁性焼鈍やアルミダイキャスト用金型の熱処理を手掛けていましたが、2年後には手狭になり、新たに群馬県玉村に群馬工場を開設しました。
その後、大手電機メーカーからのエアコン部品のろう付、コンデンサー部品の熱処理等の受注に伴って、真空炉をはじめ新しい設備の導入を進め、技術の向上にも積極的にチャレンジしていきました。
また、事業の拡大とともに関西方面からの受注も増加したため、滋賀県に2つ目の工場として滋賀工場の操業を開始しました。1970年代には防衛・航空機関連業界にも進出し、1977年には民間機のボーイング社品質規格(BAC)の認定を取得。B727部品の熱処理を行うなど特殊工程としての高い信頼性が要求される部品を、今日まで提供し続けています。
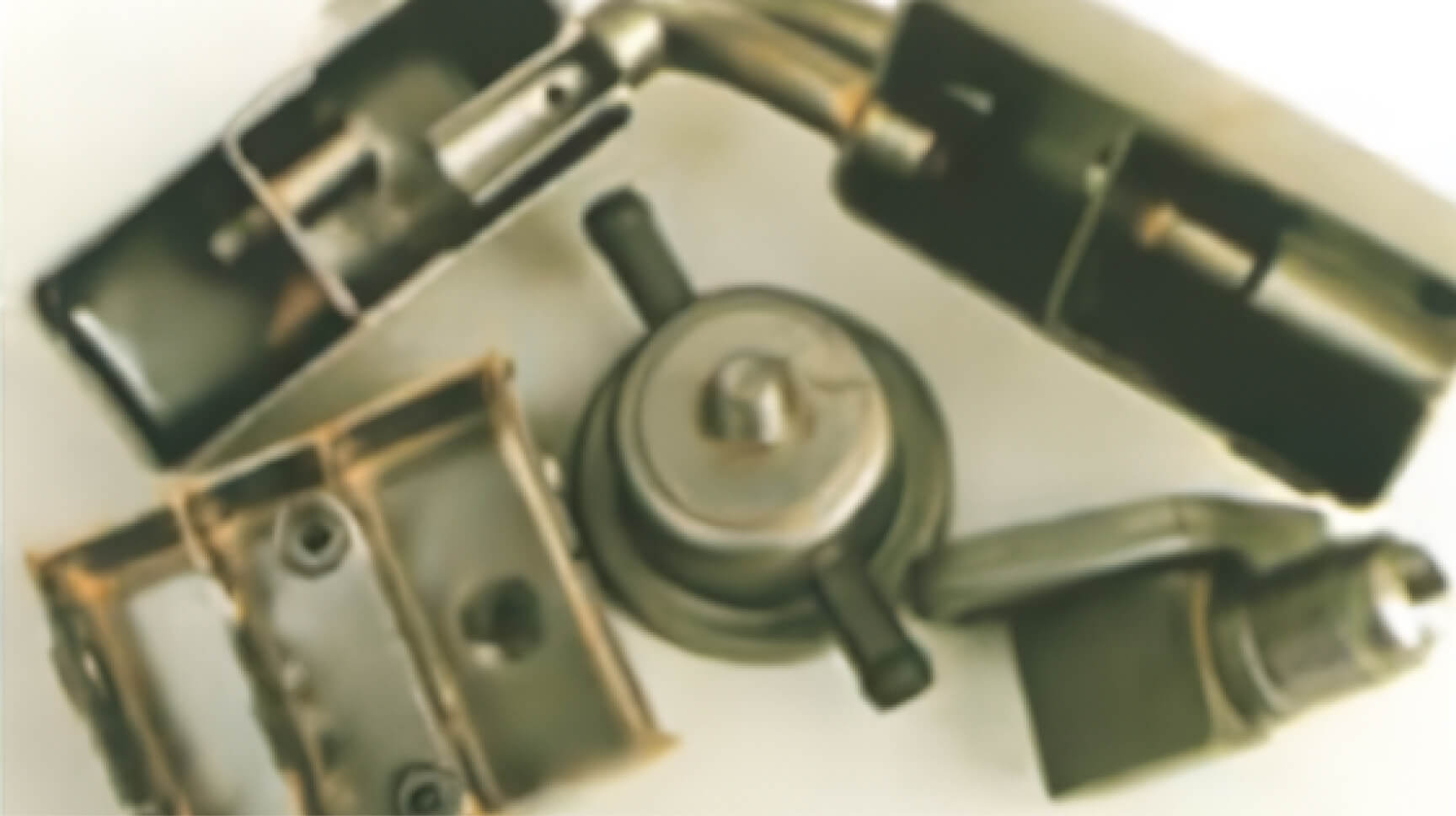
家電部品(エアコン)のCuろう付
上部左右はサクションマフラー(コンプレッサー)
1980-90年代
展開期
新しい加工技術「HIP」への展開
1980年代に入っても事業の拡大は続き、新たに3箇所(神奈川、茨城、姫路)に生産拠点を増やしていきました。
一方で、新しい熱処理技術として「HIP(熱間等方圧加圧)処理」が登場します。
HIP処理とは、高温と高圧の相乗効果を利用して、拡散接合や焼結、内部欠陥を除去する加工技術です。従来の熱処理・接合では得られない、高い信頼性の求められる分野が拡がるなか、金属技研にとっては必須の技術だと着目し、1984年に当時の日本では先端技術であったHIP装置を滋賀工場に導入しました。
HIP技術は、ガスタービン・航空機用精密鋳造品の内部欠陥除去や、粉末ハイスの焼結処理など、多様な製品に活用されていきます。またHIP技術を高めるため、1989年には「HIP開発センター」を設置。キャニング技術を高めていき、金属圧延用複合ロールの製造技術では、特許を取得しました。
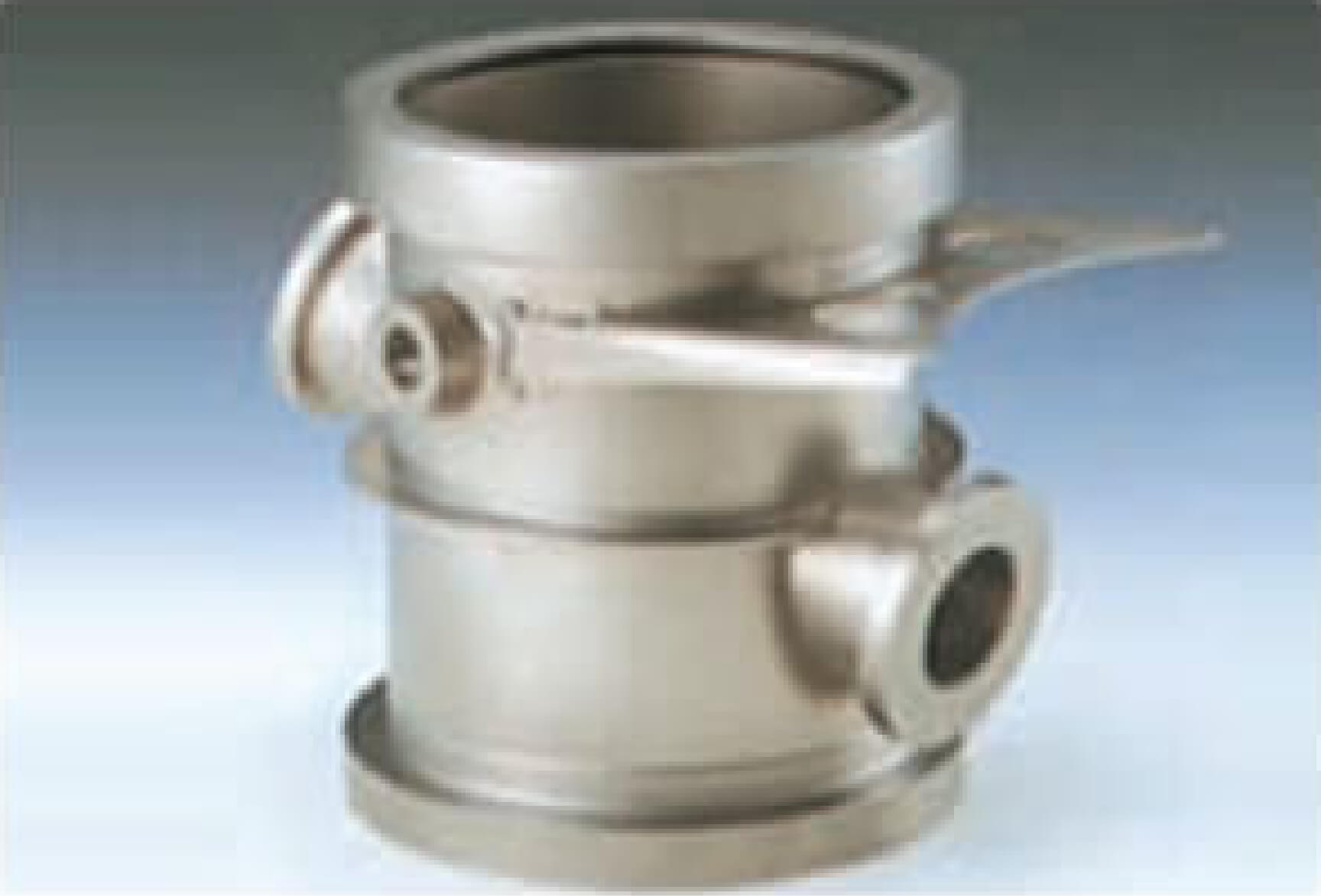
航空機部品Ti-6Al-4Vのろう付(F15J用ボディバルブ)
1990年代
転換期
「モノづくり」事業への挑戦
「最新技術をいち早く習得して、顧客に最適提案する」というビジネスモデルを確立した金属技研。HIP処理の需要が増えていくなか、顧客ニーズの多様化に伴い1993年には大型部品に対応すべく「Mega-HIP」を群馬工場に導入するなど、積極的な投資を続けていきました。
しかし、時代はバブル崩壊による不景気の真っ只中、金属技研もその煽りを受けることとなりました。
厳しい時代の流れのなか、姫路工場には大型MC(マシニングセンター)やホットプレスを、滋賀工場には超塑性成形(SPF)装置の導入を果たし、これを機に金属技研は、熱処理の受託加工からその前後工程を包括する「モノづくり」を提供する企業へと成長を重ねていきます。
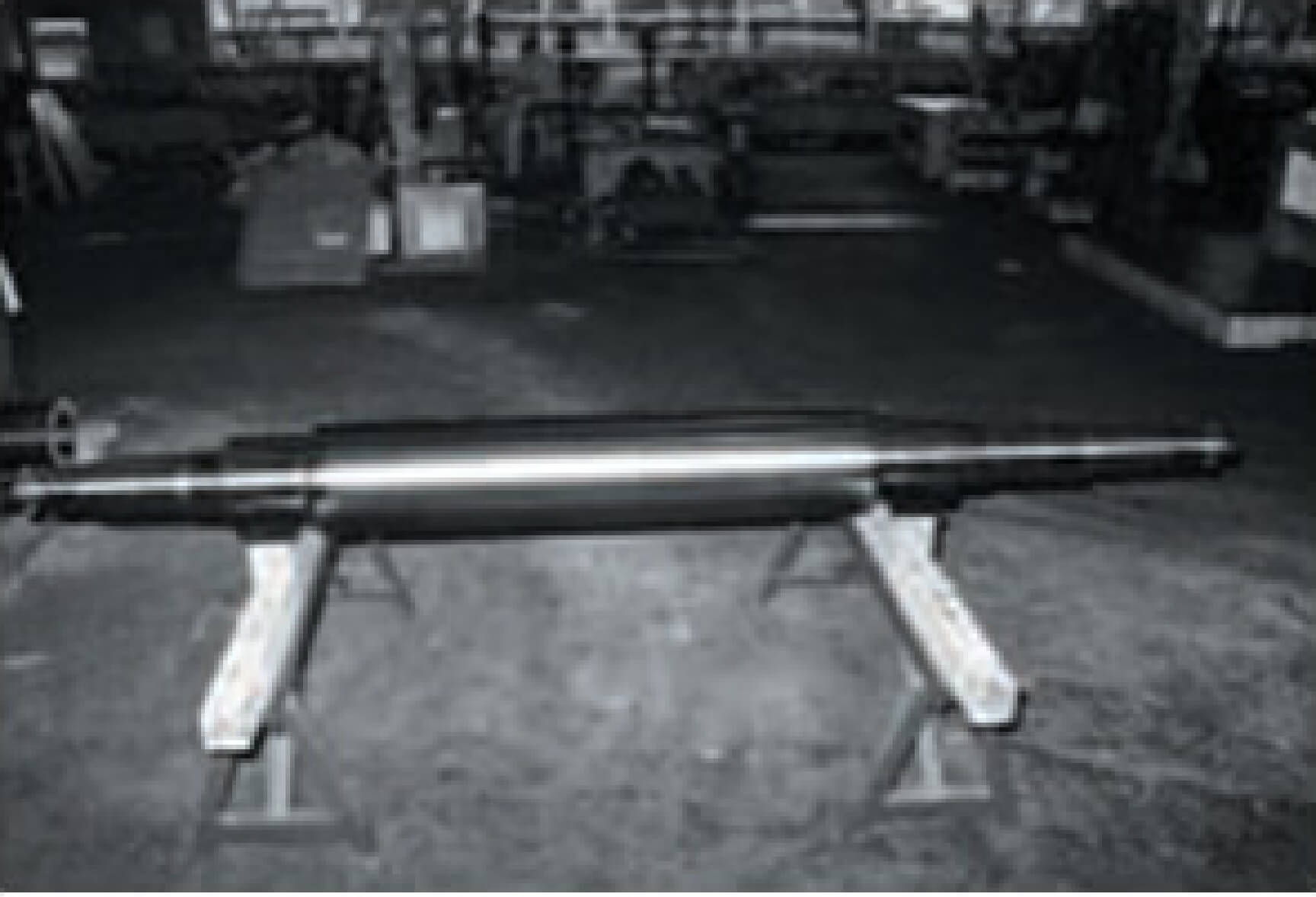
超硬材料粉末冶金(製鉄用の耐熱・耐腐食超硬ロール)
2000年代
新生期
上流から下流まで一貫体制の確立
金属技研の新たなチャレンジは、2000年代に入ってからも続きます。今話題の3D積層造形も、2001年に金属積層造形装置をいち早く茨城工場に導入しました。また、顧客が必要とする装置や部品のニーズを実現するためには、設計段階からの参画、最適素材・加工法の開発、分析・解析が必要となることから、神奈川工場内に「テクニカルセンター」を設置。さらに、2010年にはHIP技術の世界的需要増に対し、世界最大のHIP装置「Giga-HIP」を姫路工場に導入しました。
また、体制面でもうひとつの大きな変化としては、以前から加速器をはじめ科学分野には部品供給をしていましたが、顧客要望により設計・解析・製造・組立を一環で行う「エンジニアリング事業部」(現 技術開発本部)を新たに設立して、装置メーカーとしても科学分野に貢献できるようになりました。
一方、海外需要先である中国からのHIP処理依頼の増加に対して、2010年には初めての海外拠点として、中国蘇州に現地法人坂上金属技研(蘇州)有限公司を設立し、2013年に稼働を開始しました。
2011年には、将来の航空機需要に対応するために、MRO事業に参入すべく千葉工場の操業を開始しました。2012年には、成田工場において、Pratt & Whitney社からJT-8D修理事業(DPS)を継承。FAA、EASA、JCABを取得して、本格参入を推進しています。
モノづくりの上流から下流までの一貫した生産体制を備える金属技研。これからも“the metal solution”のもと、金属に関わる多くのソリューションを提供し続けてまいります。
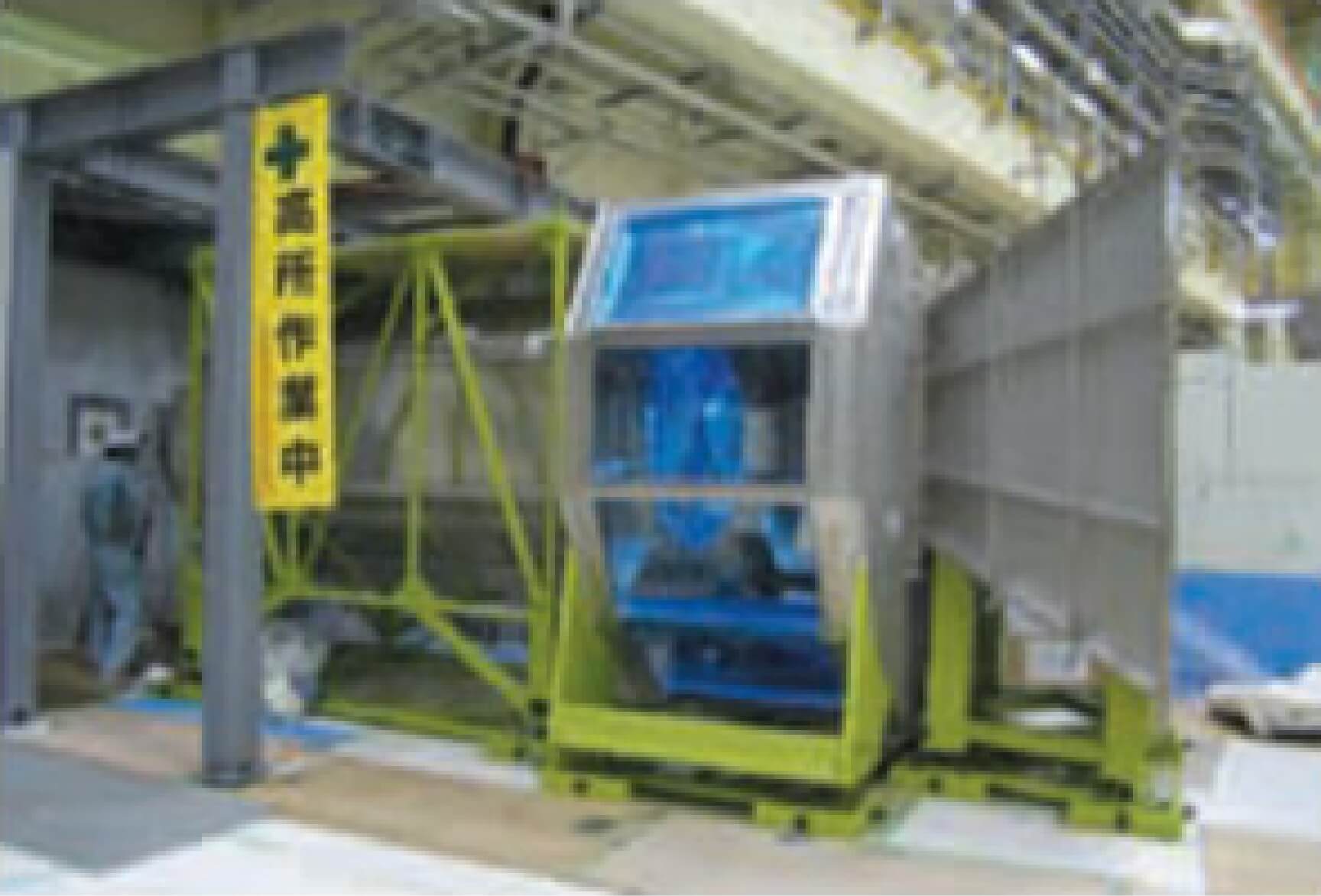
航空機部品Ti-6Al-4Vのろう付(F15J用ボディバルブ)
沿革
1960年 | 金属技研株式会社創立(東京都板橋区)、熱処理事業を開始 |
---|---|
1962年 | 群馬工場操業開始(群馬県佐波郡玉村町) |
1970年 | 群馬工場、真空炉を導入し本格的に防衛(航空)分野の事業開始 |
1972年 | 滋賀工場操業開始(滋賀県草津市) |
1974年 | 滋賀工場移転(滋賀県愛知郡愛荘町) |
1977年 | 滋賀工場、ボーイング社品質規格(BAC)の認定取得 |
1982年 | 神奈川工場操業開始(神奈川県海老名市) |
1984年 | HIP装置1号機を滋賀工場に導入、HIP事業を開始 |
1987年 | 茨城工場操業開始(茨城県水戸市) |
1989年 | 姫路工場操業開始(兵庫県姫路市) |
1991年 | マシニングセンタを姫路工場に導入、本格的に加工事業を開始 |
1993年 | 国内最大のHIP装置「Mega-HIP」を群馬工場に導入 ホットプレス装置を姫路工場に導入、焼結分野に参入 |
1999年 | 超塑性成形(SPF)装置を滋賀工場に導入、成形分野に参入 |
2001年 | 積層造形成形装置を茨城工場に導入、造形分野に参入 |
2003年 | 有限会社三泉精密から営業譲渡を受け統合 |
2006年 | テクニカルセンターを設立 滋賀工場、熱処理工程Nadcap認証を取得 |
2010年 | 世界最大HIP装置「Giga-HIP」を姫路工場に導入 エンジニアリング事業本部を設立 中国現地法人・坂上金属技研(蘇州)有限公司を設立 |
2011年 | 千葉工場操業開始(千葉県山武郡横芝光町) |
2012年 | 成田工場(FAA Repair Station)設立 米国Pratt & Whitney社からJT8D修理事業継承(DSPNetwork契約) |
2013年 | テクニカルセンター 電子ビーム積層造形装置「Arcam A2X」を導入 レーザビーム積層造形装置「EOSINT M280」を導入 |
2015年 | テクニカルセンター 電子ビーム大型積層造形装置「Arcam Q20」を導入 姫路工場 熱処理工程Nadcap認証を取得 |
2016年 | 神奈川工場 『JIS Q 9100』に金属積層造形を追加認証 茨城工場 HIP 18号機導入 |
2017年 | 土岐工場 設立 |
2019年 | 神奈川工場 医療機器製造所登録 |
2020年 | 千葉工場と成田工場を千葉工場に統合 MTC Powder Solutions AB(スウェーデン)を設立 |
2021年 | 神奈川工場 ISO13485認証取得 MRO事業撤退・千葉工場閉鎖 |
2022年 | 技術開発本部を設立 |