
HIP
Hot Isostatic Pressing
What is HIP?
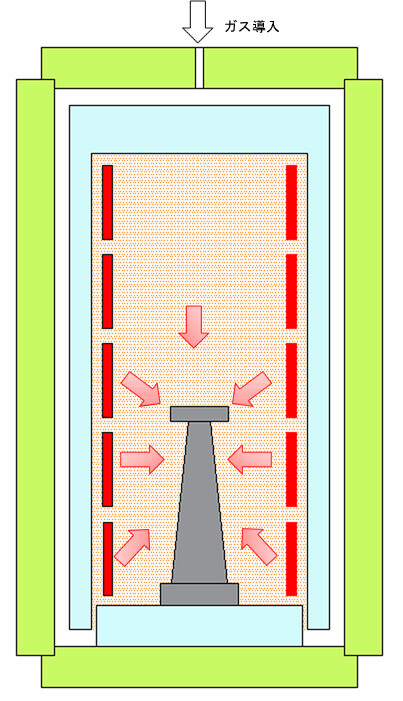
Hot Isostatic Pressing (HIP) is the technology of simultaneously pressurizing and processing materials utilizing the synergy of argon gas under high pressure and at high temperatures.
Since installing its first HIP unit in 1984, Metal Technology Co. Ltd. has steadily increased the number of HIP units and now has more than 20 machines in Japan and overseas, including one of the world's largest HIP machines called Giga-HIP.
Practical Application of HIP Technology in Subsea Pipelines
Near Net Shape (NNS) Technology: An Innovative Approach
How HIP is utilized?
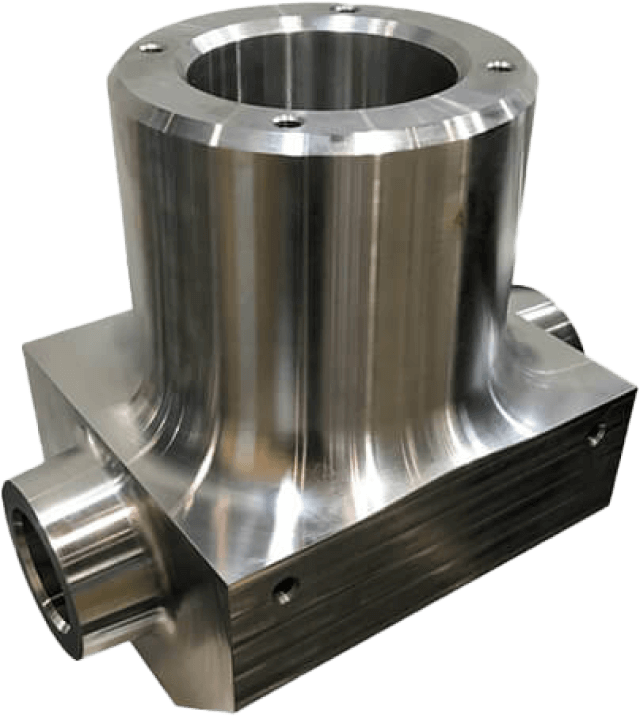
Sintering Materials
- Sintering metals that are difficult to cast.
- Manufacturing of near net shaped parts with a high level of metal purity.
- Manufacturing new materials, compounded materials and alloy materials.
- Possible to manufacture with recycled powders.
- Possible to manufacture large sized parts in one cycle and a reduction of welding or joining.
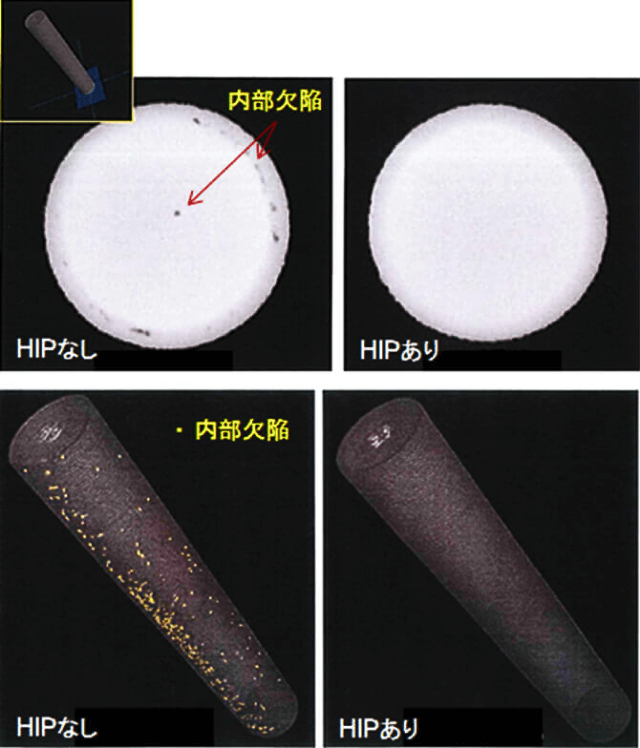
Densification of partially sintered parts / removal of internal defects
- Densification and removal of internal defects. An Improvement of reliability by densification and better mechanical properties by removing internal defects for cast products.
- Predictability, consistency of mechanical properties are improved through HIP.
- Mechanical properties show an increased tensile strength, impact strength, and improved ductility.
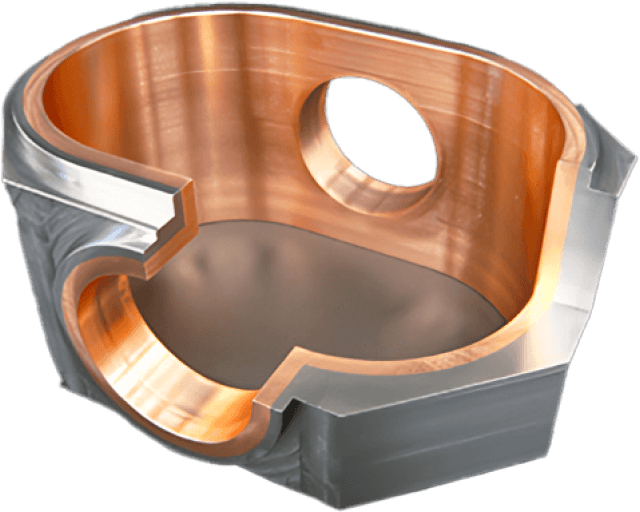
Diffusion bonding of similar and dissimilar materials
- For parts difficult to manufacture by brazing or welding.
- For parts having complex three dimensional structures.
- Bonding of dissimilar metals.
- Bonding powders and metal blocks.
- For bonding powdered materials to specific areas only.
- For manufacturing composite materials.
Applicable Fields and Materials
Applicable Fields
- Aerospace
- Semiconductor manufacturing equipment
- Electronic materials
- Energy devices
- Accelerator equipment
- Automotive-related industries
- Medical devices
- Electronic equipment
- Energy equipment
- Chemical equipment and related industries
Applicable Materials
- Electronic materials
- Magnetic materials
- Refractory materials
- Heat-resistant materials
- Corrosion-resistant materials
- Cemented carbides
- Stainless steel
- Titanium alloys
- Aluminum alloys
- Copper alloys / Iron alloys
- Ceramics
- Amorphous materials
- Resins, etc.
By combining these materials with base materials (linings), a wide variety of applications is possible.
Why Choose Metal Technology's HIP?
20+ Diverse Capacity
- With 20+ HIP units distributed globally, we can process components of various sizes and quantities.
- 15 years operation of the world-largest HIP unit, the Giga-HIP, that accomodates oversized parts and high-volume production.
- From small-batch production to large-scale manufacturing.
- With temperatures up to 2000℃ and pressures up to 196MPa.
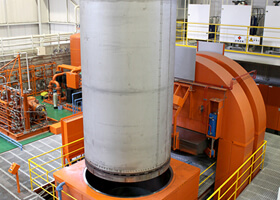
Giga-HIP
Dia.2,050mm X H4,200mm
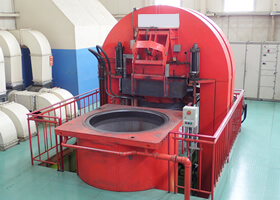
Mega-HIP
Dia.1,100mm X H2,100mm
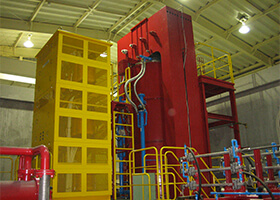
Tall HIP unit (Ibaraki factory)
Dia. 800×H3,700 mm
60 Years of Experience & Technical Excellence
- Extensice experience and a proven track record on a wide variety of similar-/dissimilar materials bonding.
- Database of accumulated technical knowledge.
- Ensure the entire manufacturing process, including pre-processing and post-processing, before and after HIP treatment.
ISO-Based Quality Management
※ISOとは? ISOとは、国際標準化機構(International Organization for Standardization)の略称であり、この組織が定めた規格を「ISO規格」と呼びます。
- ISO 9000 series accreditations and aerospace related certificates.
- ISO13485 certified
- Robust guarantee system for post-HIP
Industry-Spec Compliant
- Our HIP capabilities allow us to offer services for even the strictest standards found in aerospace and the nuclear industry, just to mention a few.
One-Stop Solutions
- From material procurement to capsule design, finishing, and inspections
- Managing every step in-house, streamlining your supply chain and enhancing cost efficiency.
HIPed samples
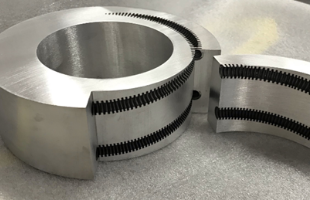
Casting product of heat resistance steel
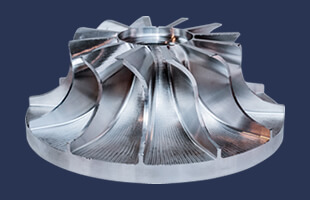
Aluminum alloy impeller
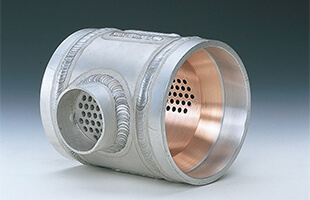
Diffusion bonding of Copper & Aluminum
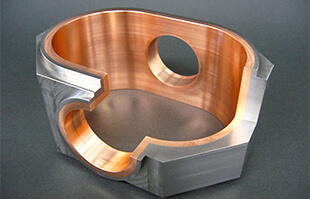
Diffusion bonding of stainless steel & Copper
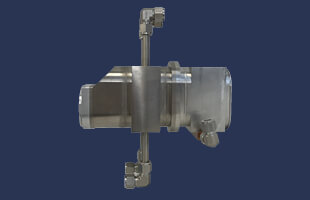
Diffusion bonding of stainless steel and titanium alloy, and aluminum alloy and titanium alloy
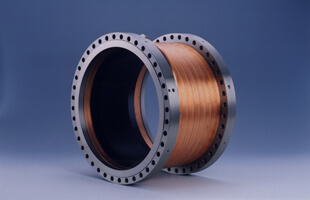