前回『積層造形製作の落とし穴』=部品設計・選定時の視野の狭さだと問題提起しました。それでは、落とし穴に落ちない為にはどうすれば良いのでしょうか? 私たちがお客様と造形検討で打ち合わせをする際によく質問する項目があります。 それは、「材料・形状が選定された理由は何ですか?」です。 お客様からは「いままで実績のある材料・形状だから」もしくは「コストが安いから」との回答を多くいただきます。当然、今までの工法だとそれがベストだったと思います。 ただ「金属積層造形ではそうならないことも多い」というのが私たちの認識です。
例えばSUS材を現状使用していても積層造形特有の形状によっては、造形時の変形を少なくし精度を得やすくなる事例もあり、その結果材料費がSUS材よりAlloy718の方が安くなることもあります。さらにSUS材と同等の強度で溶接性が良く耐食性が必要な部品であればAlloy718の方が一層コストメリットを出せる可能性があります。 また軽量化目的でAlSi10Mgを材料として使用している場合、Ti6Al4Vに置き換えるとトポロジー最適化形状で重量と強度要求が同等の上、体積が少なくなりコストダウンが出来るかもしれません。積層造形はゼロから部品を積層するため、体積が少ない方が低コスト化する傾向にあるからです。
トポロジー最適化形状は、人の経験や感覚では想像できない形なので、不安を持つ方が多くいますが、数値計算に基づいて算出した形状なので、合理的かつ信憑性の高い形状になると言われています。
上述のように、『積層造形製作の落とし穴』の回避方法の一つは『既存概念にとらわれない』ことかもしれません。 既存概念から抜け出せないと既存品のマイナーチェンジ品しか作ることが出来きません。大きなメリットが得られずにコストだけが上がり、造形メリットの恩恵を受けることなく造形検討プロジェクトが終了となってしまうかもしれません。 筆者も5年以上造形部品を検討してきましたが、今でも新しい発見があります。造形であればこんな形状が出来るかも?その形状を活かせばこんな性能が出せるかも?それであればこっちの形状の方が造形性はいいか?等々。正直、形状を考えるときは楽しくてしかたありません。
積層造形でコストダウンを検討したいということであれば一度、当社にお問い合わせください。お客様の要求を維持しつつ、金属積層造形で新しい形状のご提案の可能性をお客様と探していければと思っています。
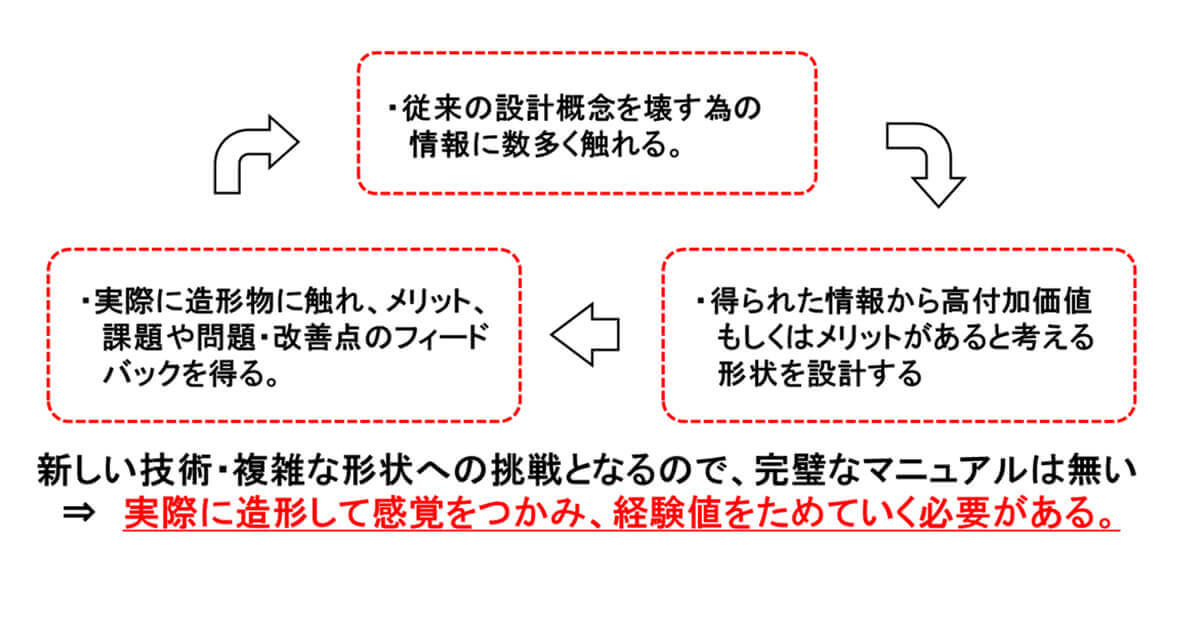