2019年7月6日東京フォーラムで行われた金属光造形加工医療機器フォーラムにおいて「金属技研が提案する金属積層造形とHIP処理」について講演をさせて頂きました。
盛況のうちにフォーラムも終わり、日本における金属積層造形に対する関心の高さが伺えました。
さて我々MTCは日頃、造形受託メーカーとして造形技術を使用して御客様にメリットが出るように色々なことを提案しています。
今回は、その中でも検討される方々が陥りやすい多くの『積層造形製作の落とし穴』について御紹介したいと思います。
積層造形のベネフィットを最大限引き出すためには?
積層造形機を使用したモノづくりにおいて、皆さんにとってベネフィットは何でしょうか?コストでしょうか?納期でしょうか?もっとシンプルに簡単に作りたい?という要望でしょうか?もちろんすべて正解です。
海外の成功事例をみても上記すべてを達成している事例は多くあります。もう一方で日本国内において上記を達成して成功している事例は、多くないように思います。
その原因の一つに『積層造形製作の落とし穴』があります。
技術的に先行しているGE社も積層造形機を使用したモノづくりでベネフィットを得るまで6年の歳月がかかったと言われております。では、彼らはどのような工程を経て成功まで実績を積んできたのでしょうか?
先ず、個々の部品だけで考えるのではなく、周辺部品もしくは全体システムまで考慮して積層造形で出来る可能性を洗い出しました。そこから、部品一体化や機能最適化、軽量化をはかり、工程短縮、納期、コスト低減を実現しました。コスト低減と表現されていますが、単に部品の製作費用だけではなく、倉庫保管の運営費、作業待ちの人件費、効率向上による設備メンテナンス時間の短縮なども含めて、総合的なコスト評価にてメリットを出しているという点も特徴です。
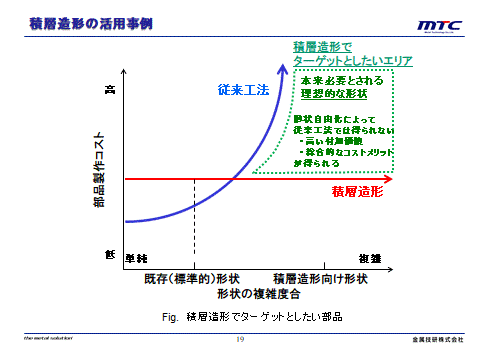
残念ながら、個々の部品を積層造形に置き換えるだけでは、費用面でコスト高となるケースが多く、積層造形のメリットを十分に活かすことは難しいです。設計変更可能、もしくは現行法でコストがかかっている部品のみを造形で製作したいという要望を、国内では多く聞きます。ただ、積層造形機のベネフィットを多く獲得するためには部署の垣根を外し全体的な目線で部品設計・選定することが必要です。検討される方々が陥りやすい『積層造形製作の落とし穴』=部品設計・選定時の視野の狭さといえるかもしれません。
次回は、その積層造形製作の落とし穴をどのように回避していくか、我々MTCでの実例を踏まえつつご紹介したいと思います。