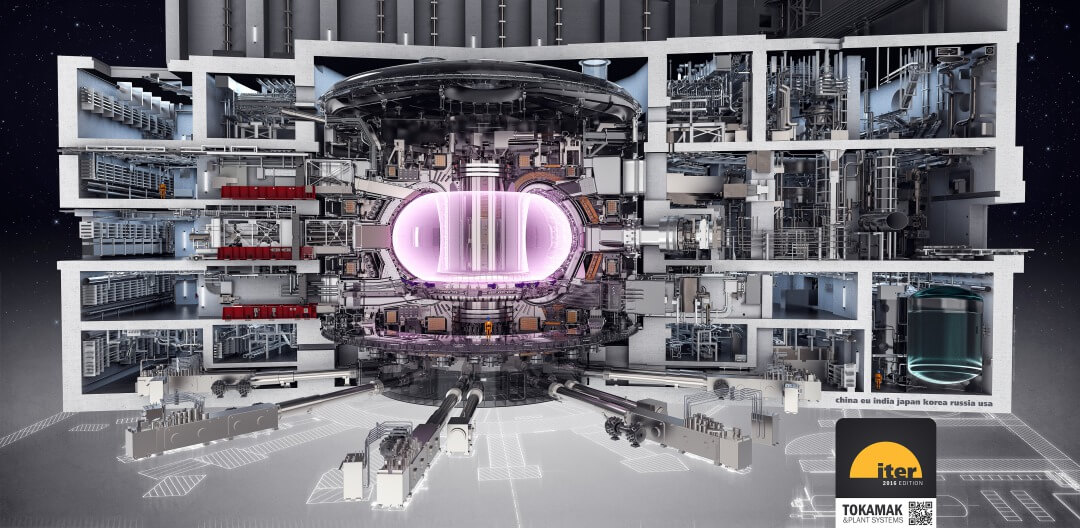
ITER, the Nuclear fusion project
Overall view of ITER (provided by ITER Organization)
【Discussion member】
■Makoto Fukuda
Plasma Facing Component Technology Group, Department of ITER Project Naka Fusion
Institute Fusion Energy Directorate, National Institutes for Quantum Science and
Technology(QST)
■Takeshi Iikura
Manager, Machining and Assembly Process Engineering Group, Production
Engineering Department, Tungsten/Molybdenum Production Division, A.L.M.T. Corp.
(A.L.M.T.)
■Masato Arai Assistant Manager, Research and Development Division, Miyoshi
Gokin Kogyo Co., Ltd. (Miyoshi)
■Senri Ohmori Metal Technology Co. Ltd. (MTC)
Nuclear Fusion Equipment Section, Engineering Department, Engineering
Division/(From March 1, 2022 Assistant Section Chief, Technical Section, Ibaraki
Plant
Chairman I would like to thank you for coming. Today is a great opportunity for all the members who play a part in the manufacture of the diverter, the core component of the ITER project, to meet. We hope to widely disseminate the efforts put in by Japanese industry. First, Mr. Makoto Fukuda, a researcher at the Plasma Facing Equipment Development Group, ITER Project Department, Naka Institute, Quantum Energy Division, Japan Quantum Science and Technology Agency (QST), will give us an overview of the ITER project. We will discuss the following topics.
Japan should develop key technologies to sustain nuclear fusion.
Mr. Makoto Fukuda
Plasma Facing Component Technology Group, Department of ITER Project Naka Fusion
Institute Fusion Energy Directorate, National Institutes for Quantum Science and
Technology(QST)
Mr. Fukuda Thanks for the introduction. The ITER project aims to
demonstrate that fusion energy is scientifically and technologically feasible.
It is a very large project involving 35 countries in 7 regions of the world, and
is currently under construction in France. As of May 2011, the project had
progressed to over 73.7%. The building is almost complete, and first plasma
(start of operation) is scheduled for 2025. After that, we plan to gradually
advance the operation, insert in-vessel equipment, and begin operations in 2035,
using deuterium and tritium as fuel. In addition to the diverter, for which we
are in charge, Japan is responsible for the main components of ITER, including
the superconducting coils, remote maintenance equipment, and radio frequency
heating equipment.
In the environment surrounding the fusion industry, the promotion of fusion has
been particularly active in various countries in recent years, and the United
States and China are planning to build DEMO and commercial reactors at a pace
that far exceeds Japan's schedule. Under such circumstances, we believe it is
important to establish proper manufacturing technology for the diverters and to
steadily proceed with the manufacturing of the diverters while adhering to the
schedule. We are currently manufacturing a prototype of the diverter for ITER
that we are procuring. After verifying and demonstrating the technology with the
prototype, we plan to start manufacturing the actual unit at the end of this
fiscal year. In addition to the 54 cassettes to be installed in the furnace, we
will manufacture a total of 58 cassettes, including 4 spare cassettes. The
current plan is to install the diverter between 2024 and 2028. The plan is to
deliver them to the facility one after another.
The most important function required of a diverter under high heat load is heat
removal. A plasma facing unit will be installed on the heat-receiving side of
the diverter. To prevent the surface from melting, the plasma facing unit is
made of tungsten, which has the highest melting point and thermal conductivity
among metals. In addition, to actively cool the diverter, not only good thermal
conductivity is important, but also the bonding technology to ensure that heat
is properly transferred and escapes. The three companies gathered here today
have important technical capabilities that are essential for the production of
plasma facing units for diverters, and they are playing an active role in this
field.
Bonding technology can be applied to Iter projects.
Chairman Thank you for the explanation. I also would like to know how A.L.M.T., which is in charge of tungsten monoblocks, Miyoshi, which is in charge of copper alloy tubes, and MTC, which is in charge of bonding them, became involved in the ITER project.
Mr. Takeshi Iikura
Manager, Machining and Assembly Process Engineering Group, Production
Engineering Department, Tungsten/Molybdenum Production Division, A.L.M.T. Corp.
(A.L.M.T.)
Mr. Iikura The Iter project is a very lofty and unprecedented international project. I think the main reason for this is that from the beginning, various senior members have brought their enthusiasm and desire to contribute to this project with their technology. I myself became the technical director of the tungsten plate in 2013 and started studying ITER. The more I learned, the more I wanted to contribute and have people use what I had made. When I visited the ITER Organization in 2018 and saw the building under construction, I was even more determined that we must not fail with what we have created and that we must create products of solid and stable quality.
Masato Arai
Assistant Manager, Research and Development Division, Miyoshi Gokin Kogyo Co.,
Ltd. (Miyoshi)
Mr. Arai We were initially approached by a major manufacturer to procure tubing materials for the diverter, but they introduced us to the company through them. We continue to develop and produce tubes. I joined the company in 2009, and when I was transferred to my current department, there was a move to completely revamp the manufacturing process. I have done most of that work in my own department, and I am eager to see this huge project through to the end.
Mr. Senri Ohmori
Nuclear Fusion Equipment Section, Engineering Department, Engineering Division,
Metal Technology Co. Ltd. (MTC) /(From March 1, 2022 Assistant Section Chief,
Technical Section, Ibaraki Plant
Mr. Ohmori We have worked with QST in various capacities. I was involved in the heat load part of the diverter and took over from my predecessor when we were considering graphite monoblocks. Now, I am continuing to work with tungsten, which is a different material with different material and physical properties, but the concept and shape are almost the same and the same bonding technology can be applied.
Reinforcement of the 3-company production system
Chairman I understand that the diverter will be installed in ITER starting in 2024, what is the current progress?
Mr. Fukuda A prototype of the diverter is under construction. The production of materials required for the actual diverter is also underway, with plans to eventually produce approximately 200,000 tungsten monoblocks. We also plan to produce approximately 1,800 copper alloy tubes, and will start manufacturing them this fiscal year. The production of materials for the actual diverter machine is also in the process of starting for the production of the actual machine.
Mr. Iikura We received the actual monoblocks from QST in January 2021 and are currently manufacturing the product. However, while we have been manufacturing on the existing line, the capacity is not sufficient for mass production. For this reason, we considered building a new line for about two years with the new line finally starting up in October, and we are now at the stage of beginning full-scale mass production.
Mr. Arai The contract was signed in January 2022. Since 1,800 units is quite a lot for production, we have expanded our production system accordingly.
Mr. Ohmori Currently, we are progressing with the tungsten monoblocks that we recently fabricated. We are in the process of trying out different furnaces to see how the color of the product and the condition of the bonding interface changes with the brazed products we have recently produced. When making large quantities of monoblocks, the number of pieces produced is limited to some extent due to restrictions on the details of the jigs and furnaces, and we would like to improve these points in the future.
Tungsten monoblocks used in diverter (center part is copper buffer for brazing)
Gathering the exceptional technical capabilities of the three companies
Divertor structure product (1/15 model of the actual model)
Three world-class companies
Chairman How competitive are these diverters internationally?
Mr. Fukuda As for copper alloy tubes, Daiwa Alloy (a Miyoshi group company) manufactures products for Europe as well and is highly competitive. As for tungsten, several manufacturers, including overseas manufacturers, have been evaluated for their tungsten characteristics, but some tungsten cracks formed when subjected to repeated thermal load. A.L.M.T. is the only company that has been able to manufacture tungsten that does not cause such damage. In addition to the outer vertical target, which Japan is in charge of, the diverter consists of other components such as the inner vertical target and the dome, which are being fabricated in other groups such as the EU and Russia. Diverters procured by other groups will also enter the phase of actual production, and we hope that we can actively expand our market share in the future.
Chairman It is impressive that A.L.M.T. is the only company that can make tungsten that has such high resistance to damage.
Mr. Iikura We have been aiming for a monoblock that will not be damaged or cracked under the high thermal load of the ITER. When we actually conducted thermal load tests for ITER, we received evaluations that our products were the only ones that did not crack or have a rough surface. Frankly speaking, at that time we did not understand why this was so, and we have been investigating various reasons. Our ability to make such efforts is one of the strengths of our company, which is involved in the entire process from tungsten powder to the final product. Finally, we were able to establish the conditions for monoblocks with almost no surface roughness even when subjected to a thermal load. We were able to establish a method of making a tungsten plate with a surface that is intentionally shattered, and now we are able to control the condition of the tungsten plate. I believe that our strength lies in the fact that we have created a monoblock that does not crack.
Chairman Miyoshi's processing and sales company, Yamato-Gokin, is also used in Europe for ITER components.
Mr. Arai In the course of our work together, we
were introduced to our company's efforts during QST's overseas presentations,
and we were approached by research institutes that produce diverters in various
countries. We have supplied tubing materials to most of the companies in where
diverters are manufactured. We also ship plates used for first walls (walls
facing the plasma). Although we are a small to medium-sized company, we believe
we are making a contribution to the world.
The cooling tubes used in diverters are joined using a combination of A.L.M.T.
and MTC technologies, but the crystal grains of the tubes become coarser due to
the high temperatures involved in bonding, and the subsequent heat load can
cause the tubes to crack. After joining the company, I was assigned to a new
position and continued to check the crystal grains of the specimens at each step
of the manufacturing process while reviewing the manufacturing process. The
bonding conditions differ somewhat from company to company and there is talk of
bonding at even higher temperatures than in Japan. Based on the current
technology, how can we respond to bonding conditions at even higher
temperatures? We are still in the process of adjusting to the optimum conditions
while continuing production, but we believe we will be able to overcome this
challenge.
Full use of database on bonding
Chairman What are the key points of MTC's technology for bonding these materials?
Mr. Ohmori A typical example of our bonding technology is Hot Isostatic Pressing (HIP), in which atoms are diffused at the bonding interface under high temperature and high pressure. In this case, brazing is used, a technology that joins with a brazing material that has a lower melting point than the material. Which bonding method to use is selected based on the condition and shape of the material, the customer's convenience, and other factors. The one we fabricated this time has a tungsten block on the outside, a buffer material inside, and chrome-zirconium-copper piping brazed on the inside. The difficulty is that copper has a large thermal expansion, while tungsten has a small thermal expansion. In the actual manufacturing process, it is necessary to control the temperature distribution inside the brazing furnace, as the bonding condition changes depending on the temperature distribution. We have a database of our past bonding experiences. Our strength is that we can check similar conditions from our database and select the most suitable one for bonding. When the temperature rises nearly 1,000°C, the gap between the set and the finished product changes depending on the state of shrinkage. There are various points to consider, such as control of the bonding interface, thermal stress control, and gaps, etc. We reduce the failure rate by checking the bonding process in advance while utilizing our extensive experience and, if necessary, thermal simulations. In the event of failure, we are proud of our ability to quickly identify the cause of the failure based on our proven track record.
We want to make something special which is made in Japan.
Chairman Nuclear fusion is a cutting-edge technology and is considered a trump card for solving various problems. What are your thoughts on ITER?
Mr. Fukuda I have been involved in research on nuclear fusion since I was a student, but at first I was told that it was a dream energy and sometimes felt that it was postponed and I did not really know when it would be realized. However, now that construction of the ITER is steadily progressing and fusion energy is close to being realized, I find this current work very rewarding. I am also attracted to the fact that diverters are equipment used under extremely harsh conditions and I am able to conduct research on equipment and materials that are exposed to such harsh conditions.
Mr. Iikura Other jobs are no different in terms of confronting challenges, but as far as ITER is concerned, it is a big project that will also solve environmental and energy problems. It is a technology that is on the verge of becoming a reality. As an engineer, I feel very happy to be involved in this project. The full-tungsten diverter is also the result of research conducted by QST and other domestic professors, so I would like to contribute to the development of this project as much as possible in an all-Japan effort, while keeping these professors in mind.
Mr. Arai This is such a big project, but the plan was delayed because of ITER and I wondered if it would take shape properly by the time I left the company, but the schedule is actually coming into view. It is very rewarding to be able to see it in action myself in the end. When I get older, I can say, "That was a job my company did. That was a project I was involved in." I am very much looking forward to being able to say so.
Mr. Ohmori I am deeply moved when I think that the products I worked so hard to create will be delivered to the superconducting fusion experimental device "JT-60SA" or incorporated into ITER, which I see in documents and other materials. I originally came from a background in biology, and I started out not knowing anything about nuclear fusion, but I find it rewarding as a field where I can satisfy my intellectual curiosity.
Mr. Fukuda The diverter will now finally enter the phase of actual production. We believe that we will need to solve different barriers from the prototype fabrication phase, such as mass production of materials and equipment, quality control, and other issues, and we will continue to steadily procure these items with your cooperation. In addition, the next phase of ITER will require the demonstration of power generation using fusion energy, and we will need the cooperation of the companies that have gained experience with ITER in that phase as well. We continue to believe in the power of all of you.
Chairman Thank you very much for your valuable and inspiring talk today.