金属3Dプリンターとは、3次元のCADデータに合わせて金属の粉末やワイヤーを溶かし固め、一層ずつ積み上げていくことで3次元の金属部品を造形する装置のことです。 金属3Dプリンターでは、切削・鋳造・鍛造といった従来の加工方法では造形できない複雑な形状を鋳造型や金型、加工治具を使用せず効率的に金属部品を製造できます。
ただし、金属3Dプリンターは、造形の方式やサイズ、機種によって製品の仕上がりが異なります。使用用途をヒアリングした上で、品質要求に耐えうる、希望通りの金属部品を手にするためには、金属3Dプリンターの基礎知識が欠かせません。
本記事では、金属3Dプリンターの方式や特長、活用事例をご紹介いたします。
金属3Dプリンターとは
金属3Dプリンターとは、3次元のCADデータに合わせて金属の粉末やワイヤーを溶かし固め、一層ずつ積み上げていくことで3次元の金属部品を造形する装置のことで、金属積層造形(Additive Manufacturing)とも呼ばれています。
金属3Dプリンターの種類にもよりますが、チタンやアルミニウム、ステンレスなど、様々な金属素材を材料に使用できます。
金属塊を削る切削加工、鋳型に金属を流し込んで固める鋳造といった従来の金属加工と異なり、必要とする部品形状を直接成形できるため、造形の難しいメッシュ構造や中空構造、破損した金属部品の肉盛りなどにも対応可能です。
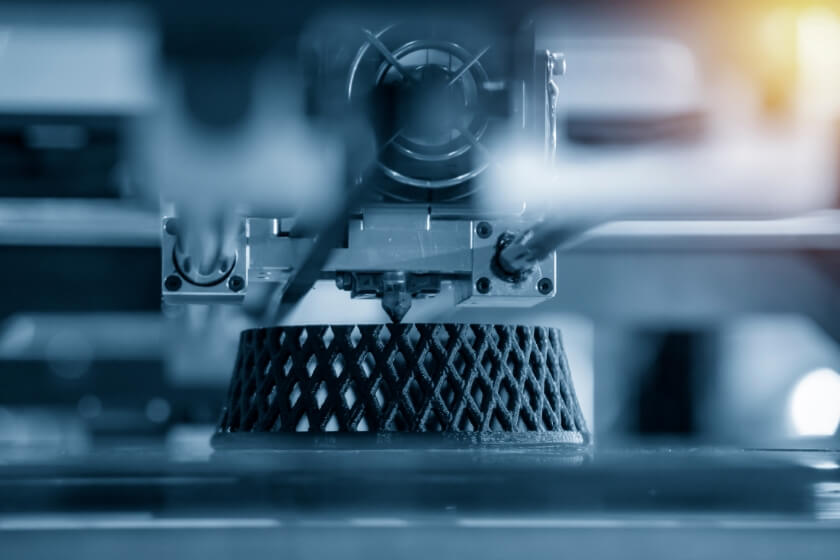
金属3Dプリンターの方式・種類と仕組み
金属3Dプリンターは、金属の粉末やワイヤーを必要形状へ積み重ねる際に利用する技術の違いによって、造形の方式がいくつか存在します。
- パウダーベッド方式
- 指向性エネルギー堆積法
- FDM方式
これら3種類の特徴と違いをご紹介します。
01. パウダーベッド方式
パウダーベッド方式(Powder Bed Fusion:略称PBF)は、10μm~100μmほどの微細な球状の金属粉末を平らに敷き詰め、レーザーや電子ビームを必要なところに照射することで、金属を溶かし、1層ずつ積み重ねていく方式です。
レーザーを使うタイプの装置は、電子ビームの製品に比べて表面の滑らかな造形が可能で、電子ビームの製品は、大型形状を効率よく造形することに向いています。同じパウダーベッド方式でも、得意不得意や造形できる金属が異なるため、多少の注意が必要です。
金属3Dプリンターの中ではパウダーベッド方式が最も普及しており、国内外の様々なメーカーから装置がリリースされています。パウダーベッド方式の特徴は、造形したい部分にのみに局所的に熱を加えるため、その周囲のパウダーは融解するほどの温度にはなりません。そのため造形部分以外の周囲のパウダーを再利用できる点にあります。
ただし、「底面から1層ずつ重ねていく」という金属3Dプリンターの仕様上、オーバーハングしている部分がある場合は、サポート材と呼ばれる支えを部品と同時に造形し、造形工程終了後に除去する必要があります。
サポート材の設計は形状や材質や装置、造形条件ごとに異なるので、最適なサポート設計が出来るか否かで仕上がり品質が変わってきます。
02. 指向性エネルギー堆積法
指向性エネルギー堆積法(Directed Energy Deposition:略称DED)は、中心からレーザーを、レーザーの周囲からは金属粉末や金属ワイヤー等の材料を供給し、供給した材料を熱で溶かして固める金属3Dプリンターの方式です。
パウダーベッド方式と異なり、「金属粉末を敷き詰めている範囲内でしか造形できない」という制限がないため、大型の造形物も製造できます。
また、「レーザークラッディング」といって、破損・摩耗した既存の金属パーツの表面に肉盛りをして補修したり、金属によるコーティングを行ったりできる点も、指向性エネルギー堆積法の特徴です。
03. FDM方式
FDM方式は、Fused Deposition Modeling(熱溶解積層方式)の略語で、いわゆる樹脂製3Dプリンターの印刷方法を、そのまま金属材料でも利用できるようにした方式です。金属粉末と、熱を与えると柔らかくなり、冷えたら固まる「熱可塑性樹脂」を混ぜたものを押し出し、1層ずつ重ねて造形します。
ただし、出力された造形品には樹脂が含まれているため、専用の溶剤に漬け込んで樹脂を溶かしたり、高温で樹脂成分を焼き飛ばしたりする「脱脂」という作業を行った後、焼結して強度を高める必要があります。
脱脂によって樹脂が流れ出し、焼結する過程で体積が20%ほど収縮するため、FDM方式で金属部品を製造する場合、必要な寸法よりも大きなサイズでの造形が必要です。
パウダーベッド方式や、指向性エネルギー堆積法の金属3Dプリンターに比べて価格が安いため、小規模な導入に向いていますが、造形品の密度や脱脂によるサイズの収縮率管理といった課題を抱えています。
金属3Dプリンターの用途
金属3Dプリンターは、航空機・自動車・自転車・医療など幅広い分野で活用されている技術です。
製造業の世界では、3次元CADと解析技術の進化や3Dプリンターの普及によって、従来の金属加工技術では実現できない「内部に複雑な構造を備えた一体成型のパーツ」や「加工の難しさから複数に分割していたパーツの一体化」などを設計できるようになりました。
樹脂3Dプリンターのパーツでは強度や安全性の面で採用できなかった部品も、金属3Dプリンターなら強度を保ちつつ造形できるようになったからこそ、金属3Dプリンターが注目を集めているのです。
たとえば、航空業界では、元々20以上のパーツを組み合わせていた航空機のジェットエンジン用燃料ノズルを金属3Dプリンターで一体化した結果、部品の軽量化だけでなく、それまで不可能といわれていた燃費の向上まで実現しました。医療分野でも、歯の形状に合わせた金属部品、人工関節など複雑な形状の造形で活躍しています。
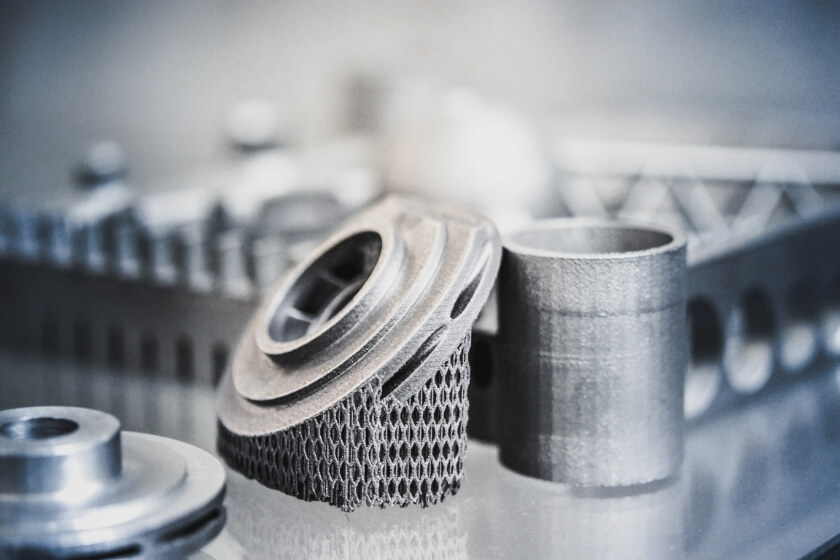
金属3Dプリンターのメリット
他の金属加工・成形技術と異なる金属3Dプリンターの特長は、以下の3点です。
- 強度や耐久性に優れた金属部品を製造可能
- 工程の集約化により短納期での製造が可能
- 造形向きな最適設計を活用することでコストダウンと製作時間の削減も実現
金属で部品を製造できるため、樹脂素材では耐えられない強度・耐久性を持たせられますし、小規模ロットでの試作や短納期の製造にも対応可能、さらに金属材料を無駄なく利用することで、コストカットや制作時間の短縮も実現しています。
強度や耐久性に優れた金属部品を製造可能
金属3Dプリンターの特長1点目は、ラティス構造を始めとした、3Dプリンターでなければ製造が困難な形状・構造の金属部品を出力できる点です。
3Dプリンターや3次元CAD、解析技術の進歩によって、今まで設計者が思いもよらないような形状が生み出せるようになり、さまざまな業界で「従来の部品よりも耐久性が高く軽量な部品」が生み出されるようになりました。
これらは、チタンやニッケル、アルミニウム、ステンレスなど幅広い金属を材料に用いて出力するので、強度や耐久性を保ちつつ部品の軽量化や一体化を実現できます。
工程の集約化により短納期での製造が可能
工程の集約化により金属3Dプリンターの特長2点目は、短納期での部品製造に対応できる点です。
これの一つの事例として、構造の一体化が挙げられます。従来の金属加工・造形では、複数のパーツを組み合わせる必要があるので、どうしても工程が長くなり、その都度手配や検査をする必要があります。ただ、金属3Dプリンターなら最初から一つの製品とした状態で一体で造形できます。金属部品を一体化することによって、製造コスト・工程の削減や溶接工程で考えられる強度の低下も防ぐことが出来ます。
コストダウンと製作時間の削減も実現
金属3Dプリンターの特長3点目は、造形向きな最適設計を活用することで製造部品のコストダウン、並びに製作時間の削減も実現できる点です。
金属3Dプリンターは、3次元CADデータを直接造形します。そのため、金属部品として欲しいパーツのCADデータさえあれば、治工具や試作型の作成が不要です。
3次元CADデータを変更すれば、部品の微調整もできるため、試作段階での金型調整や、仕様変更に合わせて治工具の新規作成工程も省略できます。
また、切削の場合、大きなインゴット(金属の塊)を購入してから、不必要な部分を大量に切り落とすことになってしまうので、材料のコストが高くなりやすいです。
しかし、金属3Dプリンターを用いて金属部品を直接出力すれば、必要最低限の金属材料で部品を造形できるため、材料のロスを抑えられます。
金属3Dプリンターによる造形品の強度
金属3Dプリンターを活用するメリットについて、おわかりいただけたかと思います。
ただ、気になるのが、金属3Dプリンターで作製した部品の強度なのではないでしょうか?仮に、求める強度がなければ、部品として活用しようとしても用途が限られてしまいます。
金属3Dプリンターの素材強度
金属3Dプリンターの材料は主に、下記のような金属の粉末もしくはワイヤーです。
- ステンレス鋼(SUS316L、SUS630など)
- チタン合金(Ti-6Al-4Vなど)
- アルミニウム合金(AlSi10Mgなど)
- ニッケル超合金(Ni Alloy718など)
- コバルトクロム合金(CoCrMoなど)
金属3Dプリンターのメーカーなどから材料特性値が公表されているものもありますが、研究開発中の材料ではなく正規材料として市販されている多くの材種では、鋳造や圧延などの従来の工法で作製した同種材料と遜色がありません。
このため、正しく造形することが出来れば金属3Dプリンターで作製した素材強度の低下は、ほとんどないと考えられます
金属3Dプリンター部品の強度
では、これらの材料を用いて実際に造形した部品の強度は、問題がないのでしょうか?
結論からいえば、素材として従来の工法で作られた素材と同等、あるいはそれ以上になる可能性があったとしても、部品品質として比較すると単純に比較することはできません。
というのも、選択する造形方法や部品形状、造形後の表面状態、後熱処理などにより、強度が変化するためです。
特に、繰り返しの応力(荷重)がかかった場合の疲労強度については、金属3Dプリンター特有の表面粗さによって従来の工法に比べて低い可能性が指摘されています。
このため、長期間の使用や厳しい環境下で使用する際には留意する必要があります。
金属3Dプリンター部品の強度品質を高めるには?
金属3Dプリンター部品の疲労強度は、後処理を施す事で向上させることが出来ます。
疲労強度を向上させるためには主に2つの原因を取り除く必要があります
原因1:内部にある欠陥
一つ目の原因は金属3Dプリンター部品内部にある欠陥です。
これらはHIP(Hot Isostatic Pressing)処理で欠陥を潰し、その後適切な後熱処理を施すことで改善させること出来ます。
原因1:金属3Dプリンター特有の表面粗さ
二つ目の原因は、金属3Dプリンター特有の表面粗さです。
これは、ショットピーニング、研磨、切削加工などで部品表面の凹凸を慣らしすことでで改善することが出来ます。
2つの原因を取り除いた場合、たとえばTi6Al4V合金では、圧延材ど同程度の疲労強度まで改善することが出来ます。
金属技研の強み
業界トップクラスの技術力を誇る金属技研は、金属3Dプリンターを用いた造形に関して、以下のような強みを持っています。
- 設計から品質保証まで自社で一貫して行える
- お客様のメリットを高める形状・構造の設計サポートができる
- 後熱処理をすることで、造形特有の課題も改善できる
- 金属3Dプリンター造形で『JIS Q 9100』の認証を取得
金属技研の強みを、順番に見ていきましょう。
設計から品質保証まで自社で一貫して行える
金属技研は、金属加工・造形のプロであり、金属3Dプリンターの専門家です。
そのため、単に受注した製品を金属で製造するだけでなく、製品の構造解析や成分分析を含む事前検証から、造形メリットを得られる形状の提案、造形後の熱処理に仕上げ・検査まで、最終製品の納品に必要な工程のすべてを一社で提供しています。
製造した造形品の強度試験も含め、製品の相談から納品まで必要な工程を自社で一貫して行えるため、受発注のコストを最小化することが可能です。
お客様のメリットを高める形状・構造のサポートができる
金属3Dプリンターの強みは、従来の造形方法では実現できない部品形状ができる点にあります。
ただし、金属3Dプリンターの性能や金属材料の性質を把握していないと、強度を保ったままの軽量化やお客様の要望をクリアすることは出来ません。
その点、金属技研は金属にも金属加工にも精通する企業です。お客様の悩みや製品の使用環境を丁寧にヒアリングし、金属3Dプリンターだからこそ実現可能な3次元ラティス構造やトポロジー最適化構造、一体化のアイデアなどを提案することができます。
後熱処理をすることで、造形特有の課題も改善できる
金属3Dプリンターは、金属を熱して融解させ、冷却して積層するという機能上、造形物の内部に欠陥が生じやすいです。
そのため、金属3Dプリンターで製造した製品のうち、高い構造強度が求められていたり、高速回転部品、振動がかかる部品においては内部欠陥を除去するための後熱処理が推奨されています。
当社の場合、ガスを使って高温・高圧を均等にかけるHIPという装置を利用して造形物の緻密化を行うことが可能です。
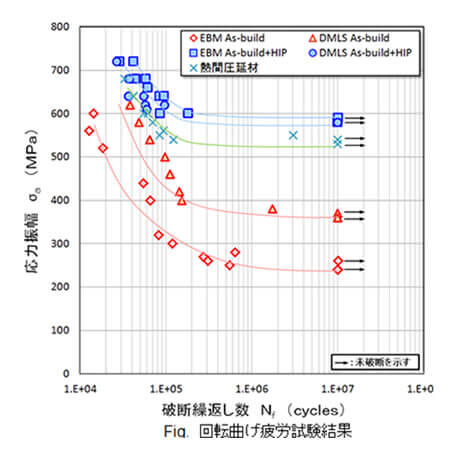
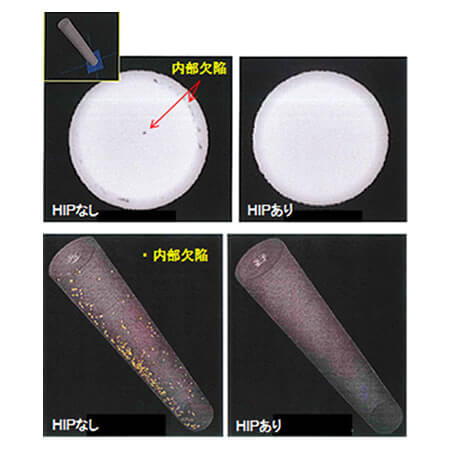
HIPについて詳しく知りたい方は、下記ボタンよりご覧ください。
金属3Dプリンター造形で『JIS Q 9100』の認証を取得
金属技研は、2016年に金属3Dプリンター造形で『JIS Q 9100』の認証を取得しました。
JIS Q 9100は、わずかな強度の劣化や加工のミスが大事故につながる航空宇宙・防衛産業用の品質マネジメント規格です。
金属技研では、金属3Dプリンターで使用したリサイクル粉末の劣化や各工程の管理する品質管理と、それらを追跡し管理できる体制を整えることで、航空宇宙・防衛産業レベルの品質管理を提供しています。
金属3Dプリンターを用いた加工事例
金属3Dプリンターは、さまざまな分野で利用されている技術です。
しかし、具体的にどういった構造・形状の金属部品を製造できるのか、サンプルを見ないと金属3Dプリンターの有用性を判断できません。
ここでは、航空・エネルギー・自転車・インテリア・開発・研究・医療機器などの世界で金属3Dプリンターがどのように用いられているのか、その加工事例をいくつかご紹介します。
航空
高圧・高温への耐久性を求められる航空業界では、金属3Dプリンターの造形品が利用されています。
その一例が、タービンブレードです。
軽量耐熱合金であるTiAl製のブレードを造形し、HIP処理と機械加工を行うことで、軽量かつ高温に耐えられるブレードの製作に成功しています。
TiAlのような製作性の悪い合金も、金属3Dプリンターであれば、加工の負担と金属材料の無駄使い、両方の削減が可能です。
航空業界の加工事例は、下記ボタンよりご覧ください。
既存製品の最適化を達成した開発・研究
金属3Dプリンターは、既存製品や部品の形状もしくは特性の最適化にも向いた技術です。
たとえば、当社では既存のボールジョイントを詳細に分析し、構造上不要な部分を削除、必要な強度を計算した上で軽量化と形状を一体造形することによって、機能性や強度を保ったトポロジー最適化形状を実現しています。
その結果、製作工数・部品の点数・重量・コスト・工期のすべてを改善することに成功しました。
開発・研究分野での事例は、下記ボタンよりご覧ください。
まとめ
金属3Dプリンターは、既存の技術では加工が不可能だった形状や構造の金属部品を製造できる革新的な金属加工・造形技術の一つです。
ただし、金属3Dプリンターによって対応できる金属材料の種類や造形品の仕上がり、得意とする金属部品などが異なります。
金属3Dプリンターの特長を活かしたものづくりを行うためには、除去がしやすく熱歪みの少ないサポート材の設計ノウハウ、既存部品の分析による形状の最適化、小ロットでも大量生産でも均一の仕上がりを保てる厳しい管理体制が必要不可欠です。
金属部品の試作、既存製品の最適化や低コスト化、軽量化にご興味がある場合は、ぜひ一度、こちらの下記ボタンよりご連絡ください。
適用分野・適用材料
適用分野 | 航空・宇宙、半導体製造装置、電子材料、エネルギー機器、加速器機器、自動車関連、医療機器、電子機器、精密機器、化学機器関連など。 |
---|---|
適用材料 | 電子材料、磁性材料、高融点材料、耐熱材料、耐食材料、超硬合金、ステンレス鋼、チタン合金、アルミ合金、銅合金、鉄合金、セラミックス、非晶質材、樹脂など。また、母材とのライニングにより、組合せは多岐にわたります。 |
セミナー紹介
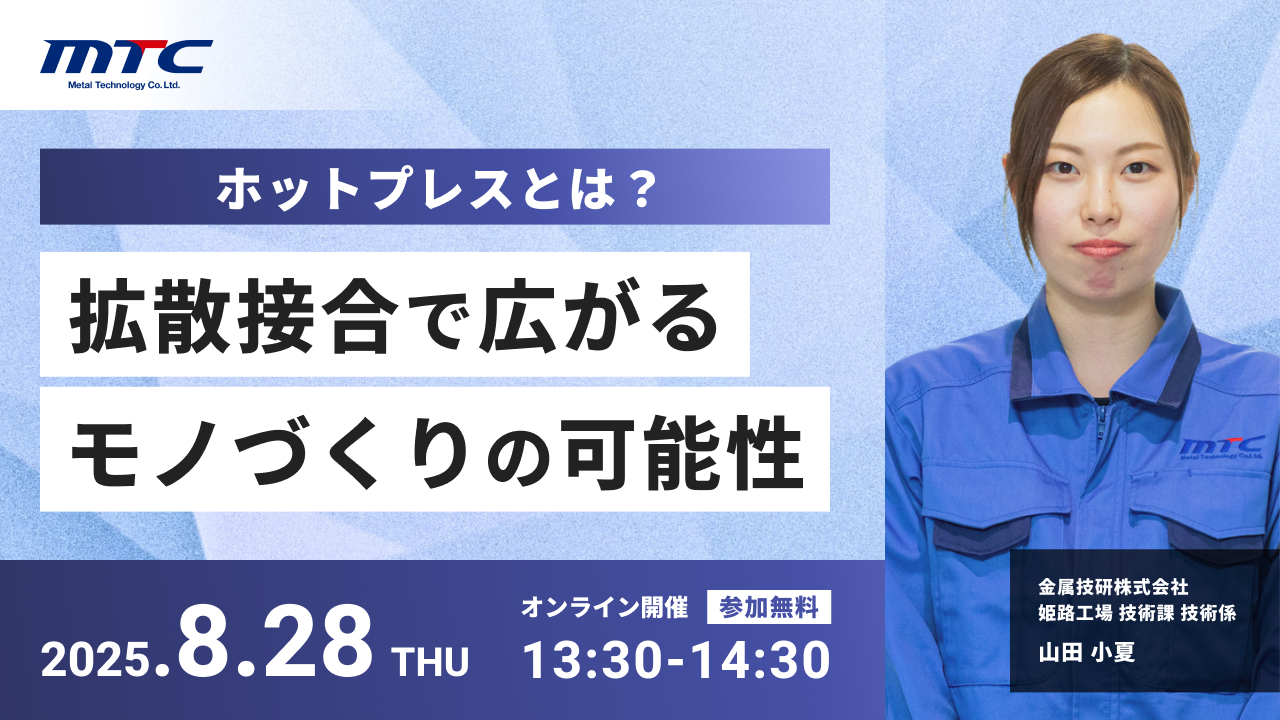