For universities and research institutions_China
More than just bonding - MTC in R&D
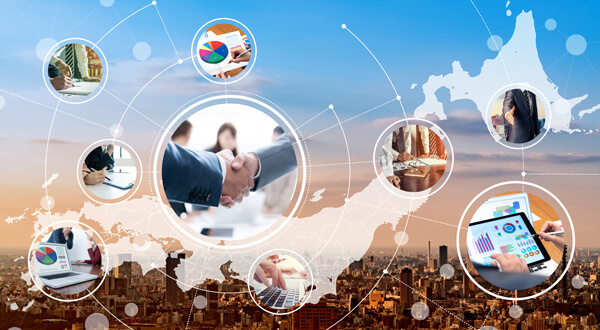
In addition to commissioned fabrication services such as bonding and brazing of dissimilar metals, MTC is actively involved in joint research and development in a variety of fields with universities and companies.
In the past we have carried out more than ten research projects and we are still activly working with five more.
As a specialist in the field of metals, MTC works alongside customers and research institutes to foster and support the investigation of the possibilities of metals.
Partners
Universities
University of Fukui, Tokyo metropolitan university, Hokkaido university, Muroran institute of technology and Tokyo Institute of Technology
Research institutions
High Energy Accelerator Research Organization (KEK), National Institute of Advanced Industrial Science and Technology (AIST) and Tokyo Metropolitan Industrial Technology Research Institute
Results
Research and development results
Project | Period | overview | More information |
---|---|---|---|
Development of die materials for processing titanium-based parts for precision medical devices | 2015-2017 | With the progress of minimally invasive treatment, the demand for molded parts of titanium alloy materials, which are difficult-to-process materials, is increasing. In this project we developed two technologies – 1) A technology for new functional alloys using graphene composites. 2) We also developed process technology for boron nitride coated film with hard properties and low friction properties. This resulted in a high performance as a metal adhesion prevention and lifetime improvement for dies which can be applied to difficult-to-forge titanium-based material. |
https://www.chusho.meti.go.jp/sapoin/index.php/cooperation/project/detail/1813 |
Development of Diffusion-bonded Cemented Carbide for game-changing Long Life Drilling Bits. An Advancement and Fusion of Manufacturing and Analytical estimation Technologies | 2016 October 1~ March 31, 2020 |
Micro Slurry jet Erosion (MSE) is an erosion evaluation method which can be utilized for evaluating material properties from the surface of erosion by impacting the surface with hard particles at high speed. By using an MSE erosion rate, the difference can be observed in the rate of erosion even on materials like cemented carbide. This technique can provide the same evaluation information as when performed by a conventional more difficult mechanical evaluation. The purpose of this research and development is to evaluate cemented carbide from this new perspective and to develop high-hardness and high-toughness cemented carbide that have even better erosion resistance. The current stage is to prepare an environment for rapid development of cemented carbide bits and create a stage of practical development. | https://www.jst.go.jp/tt/EN/univ-ip/a-step.html |
Research and Development for Robust Nickel-Based Superalloys with controlled Oxidation for Additive manafacturing. | April 1, 2019 to September 30, 2021 |
Solutions to global warming issues have broadly two approaches: The "adaptation option" and the " mitigation option". Adaptation option aims to mitigate the impact of global warming by adjusting the natural and social conditions. On the other hand, the mitigation option is intended to control the emissions of greenhouse gases themselves, and the contribution of science and technology is greatly expected. Various technological options as mitigation measures can be considered in several areas and technology, but ALCA aims to create a low-carbon society by creating energy, storing energy, carbon neutral CO2, and by reducing CO2 emissions through energy saving. ALCA's research results are expected to be implemented in the future through stepping up the R&D phase to a closer point to a practical usage. Therefore, the R&D issues of ALCA must satisfy the following three requirements. 1.There is expectation from industry. This project aims to focus on the development of Nickel-Based Super alloys with Controlled Oxygen and Nitrogen Impurities for Application to Additive Manufacturing. |
Disclosure not possible due to the project being ongoing. |
Development of sharp, high-hardness tools for shearing magnetic steel sheets for various motors to support an electrified society | July 1, 2019 to March 31, 2022 | Higher efficiency of motors will be a technology that supports a fully electrified society. In motors manufactured by shearing magnetic steel sheets, strain during shearing causes iron loss. In this development, the tip of the shearing tool is sharpened to a nanometer in size to limit the shear strain region and suppress iron loss. | Disclosure not possible due to the project being ongoing. |
Development of a manufacturing technology for enlarged tungsten with ultra-heat-resistant, high-toughnes. | June 1, 2019-March 31, 2022 | In recent years, the market for organic ELDs has been expanding because of the advantages of high definition, thin, light weight, wide viewing angle, and the possibility of bending the sheet substrate instead of liquid crystal displays (LCDs), but at present, the compatibility of "low power consumption" and "low cost of the manufacturing process" has become an urgent issue. The cause is considered to be the upper limit of the operating temperature and the life time of the deposition cell heater, and to solve the problem, it is aimed that the super heat-resistant and high toughness tungsten material is enlarged, and mass-produced. | Disclosure not possible due to the project being ongoing. |
R&D project on the use of additive manufacturing of aluminum containing Steel for use in the Next Generation Energy Plant | September 1, 2020 to March 31, 2022 | With the aim of early realization of next generation energy plants such as nuclear fusion reactors and solar thermal power plants, Tokyo Institute of Technology has developed stainless steel containing Aluminum in which corrosion is almost zero in liquid metal fluids as refrigerants. Additive manufacturing materials for next-generation plants will be developed by combining this seed of technology with MTC's Additive Manafacturing expertise to solve corrosion resistance and joining challenges isssue simultaneously. By applying the additive manufacturing method which goes through the melt solidification process of metal powder continuously, the AM material is produced with a chemical composition which dramatically improves the corrosion resistance. The corrosion resistance under corrosive environment will be evaluated and the practicability of this use of metal additive manufacturing of stainless steel containing Al will be assessed. The realization of structural materials without welds weilding for which inspection is mandatory can be expected to be widely developed not only in the energy field but also in the chemical plant industry and transportation fields. | Disclosure not possible due to the project being ongoing. |
Development of Long and Short Fiber Hybrid SiC Matrix Composites | 2019 April 15 to March 31, 2020 | Although the SiC / SiC composite material by the NITE method (Nano-Infiltration and Transient Eutectic-phase), for which the National Institute of Technology holds a patent priority license, can form a dense matrix. Through joint research with Muroran Institute of Technology, we have developed a technology for manufacturing high toughness type NITE-SiC / SiC composite materials. The purpose is to manufacture a long-short fiber hybrid SiC / SiC composite material in which a carbon material is composited with a matrix to improve toughness. | Disclosure not possible due to the project being ongoing. |
查询表格
请通过下面的咨询表格与我们联系。
*您如果没有收到邮件的话,可能输入错误了。请您再次输入查询表格。